The erstwhile ICE Department contributed to indigenous engine technology in the early years of India’s industrial development
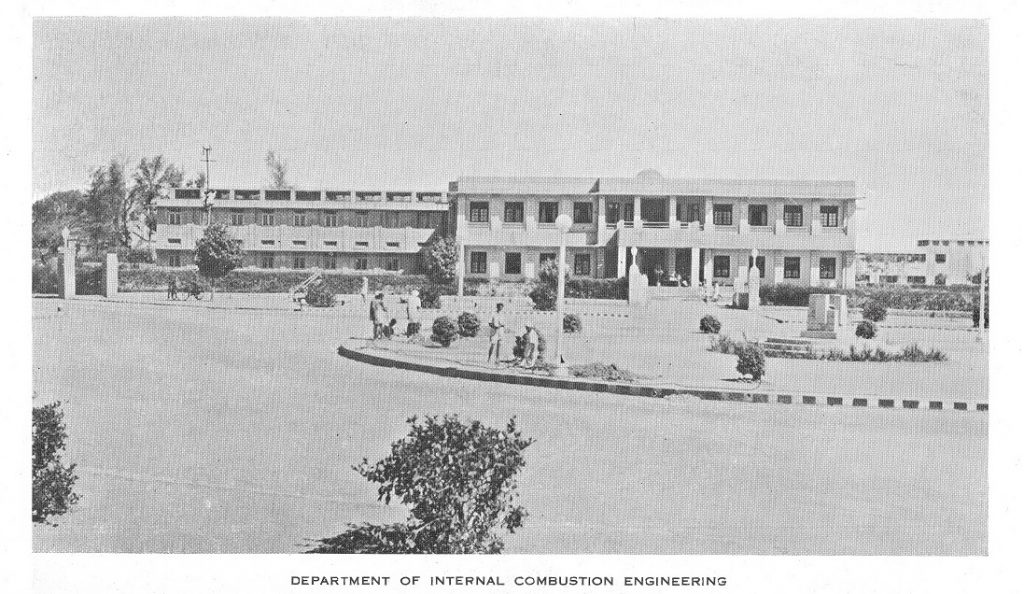
There once was a particularly popular department at IISc called the Department of Internal Combustion Engineering (ICE), and for close to a quarter of a century, the engineers there designed, constructed and tested a plethora of engines and engine accessories.
Since its initial use in driving water pumps in the late 17th century, the steam engine has been used in diverse ways for many human applications. This was purely for lack of choice; this kind of external combustion engine was cumbersome as the quantities of water required to create an adequate amount of steam could be huge. Also, though this kind of fuel was cheap, the heat generated was dangerous to work with, and leakages were common, wasting a lot of energy. In the second half of the 19th century there was a frenzy among inventors to create a heat engine that was more efficient and less cumbersome than the steam engine. Nicolaus Otto is often credited with building the first modern “Internal Combustion Engine”, although several other engineers such as Karl Benz and Rudolf Diesel contributed to its evolution. Many patents and certifications for “obtaining motive power from explosion of gases” were given out during this period. In the subsequent years, IC engines generated power to run everything from cars and airplanes to stationary power plants. Massive industrial machinery was powered by IC engines.
Machines are central to the industrial development of any nation, and machines are powered by engines.
To appreciate the complexity of IC engine research, it is useful to get an idea of how an engine works. In its most basic form, an IC engine constitutes a chamber in which a mixture of air and fuel is injected. A piston plunges inward into the chamber to create very high pressure, causing the mixture to explode. This sudden explosion drives the piston back, initiating a chain of events: a crankshaft attached to the other end of the piston rotates, leading to the movement of gears, pulleys or hammers; essentially using the energy from the heat to move things. The shapes and sizes of each of these parts, the materials they are made of, the fuel used, the force with which it is injected into the chamber, the pressure imparted by the piston, the number of chambers, the number of explosions – all these factors (and more) contribute to the efficiency with which an engine generates power and moves a machine. There can be literally hundreds of moving parts in a machine. And when you turn an engine on, you start a chain reaction that eventually ends up turning the wheels of a car, or lifting the mechanical arm of a crane, or drawing oil out from deep seas.
ICE at IISc
IISc did not enter the field of engine research until almost the end of World War II. In 1945, a new Department of Internal Combustion Engineering (ICE) was set up. It soon occupied the grey stone building at the southern entrance to the campus, which is now the Society for Innovation and Development.
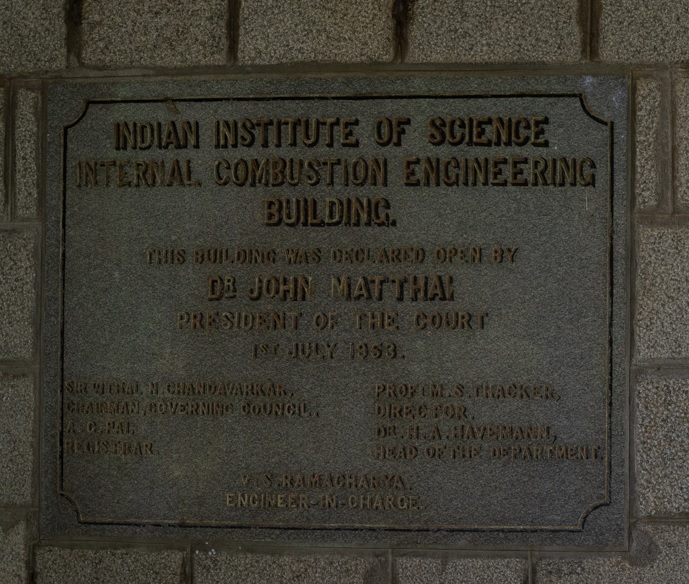
The 1944-45 Annual Reports record two developments that played a significant role in the establishment of the ICE Department. The first was the journey of Sir JC Ghosh (Director of IISc at that time) to England as a member of the Indian Scientific Mission. There, he discussed with experts from around the world about the need for new areas of research at the Institute. Upon their recommendations, he appointed Major BC Carter to teach the students at the Department of Aeronautical Engineering “the working of Internal Combustion Engines,” thus sowing the seeds of a new department. The second was the decision of the Institute to start post-graduate programmes in Heavy Engineering, Power Engineering, Designing of Machinery, and Chemical Engineering, “in view of the post-war plans for the proper development of the resources of the country.” Steps were taken to raise a generation of well-trained, confident engineers who
could stand up with the best in the world.
In 1945, a new Department of Internal Combustion Engineering (ICE) was set up
From the get-go, researchers at ICE worked actively with their industry counterparts, testing and designing various types of engines and their components, housing them in a large hangar in the west wing, according to former faculty member V Kuppu Rao. One of these, he notes, was a Derwent Mark V engine that originally powered fighter planes in World War II, which was given to the Department by Rolls Royce. Its “howl”, he says, could shatter the calm over the entire campus and the then relatively quiet streets of Malleswaram.
Many collaborative projects were carried out by ICE under the aegis of the fledgling Council of Scientific and Industrial Research (CSIR). One of these – led by HA Havemann, who succeeded Carter as the Department head, and VM Ghatage, Chief Engineer of Hindustan Aeronautics Limited (HAL) – focused on developing a fully indigenous six-cylinder engine for the HT2, India’s first aircraft used to train air force pilots. Another of Havemann’s projects centered on an engine using hot air as the working medium, which could prove useful in rural areas where organic fuels like firewood or charcoal were more abundant than gasoline or diesel.
For the next 20-25 years, engineers at ICE invested efforts to indigenise foreign engines, to develop new engines using local material and indigenous fuels, and attempted to reduce the pollution that was always
associated with the use of engines.
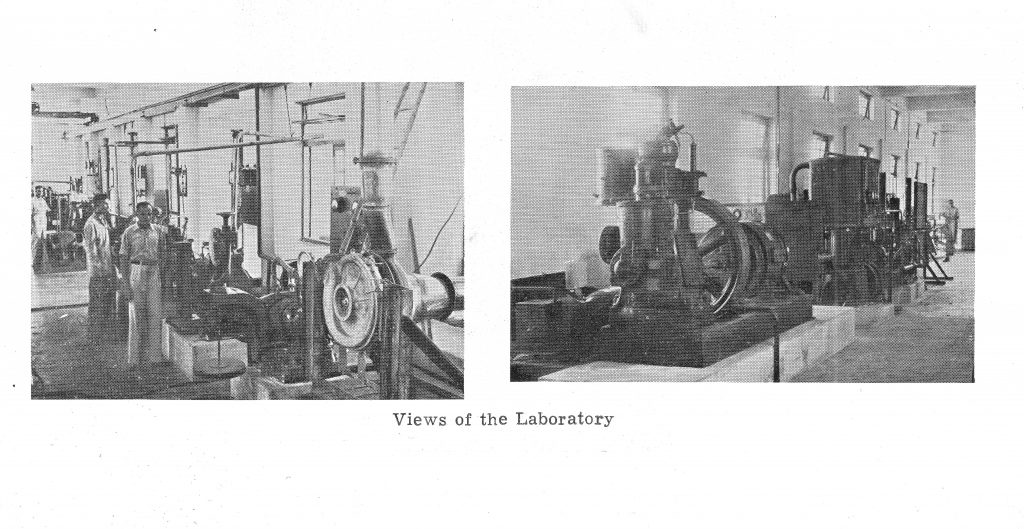
Examples of activities reported in the 1952-53 Annual Report give an idea of the diversity of the work carried out in the ICE laboratory: Testing of two Kirloskar engines for the effect of chromium plating on the piston ring, tests conducted on ‘horizontal single cylinder engines’ from Messrs Cooper Engineering Ltd to improve the geometry of the combustion chamber, development of ‘twin fuel Diesel engines’ to accept indigenous fuel and the installation and testing of a Derwent Mark V turbo-jet engine.
Indian industry at that time was rudimentary at best. Most engines and fuel were imported and expensive. The Department often received engines from outside sources for testing and analysis of parts. The Annual Reports describe how the stands on which engines were hoisted for testing often required significant realignment to accommodate foreign-made engines.
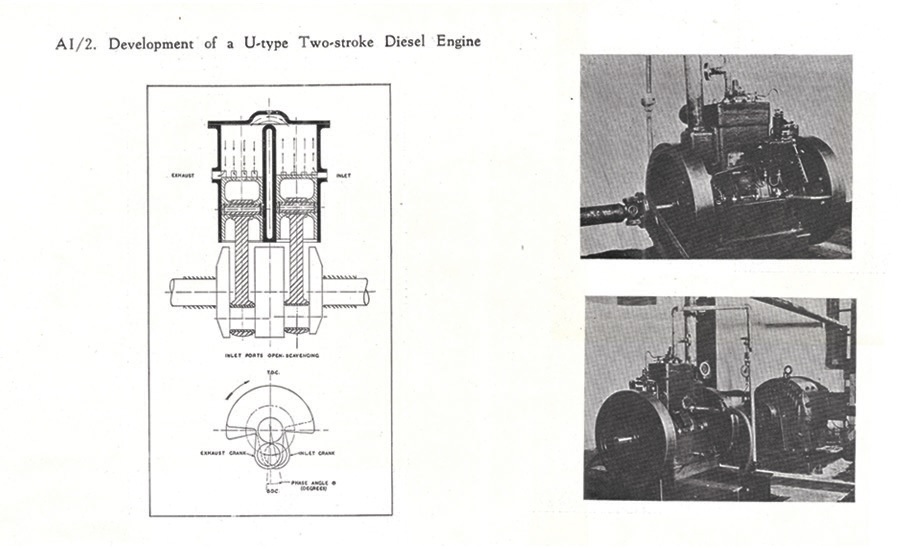
(Image: ICE brochure, 1953)
The engineers at ICE strove to create engines suited to Indian conditions. Indigenous fuels, vegetable oils and alcohol were tried out as cheaper replacements to imported mineral oil. Innovative techniques for manufacturing crankshafts were tried. Several observers have reported that in innovation and discovery, ICE researchers were at par with their counterparts in countries like Japan and Germany.
The engineers at ICE strove to create engines suited to Indian conditions
Less noise, more efficiency
Work in one area that considerably advanced the field was efforts to reduce the air and noise pollution caused by engines. N Raman, who joined the Department in the late 1960s and retired as a Principal Research Scientist in 2003, remembers how loud many of these engines were. “There are so many IC engines,” he says. “A gas turbine is also an IC engine. We had a gas turbine section. It made a tremendous noise. It could be heard everywhere, even outside the campus. Finally, it had to be discontinued.” Raman calls faculty member Manohar Munjal “one of the best in the world” in the field of acoustics; his research played a major role in reducing noise pollution. Raman himself studied tribology, the science of friction and lubricants. He worked with MV Narasimhan, a professor at ICE, on two-stroke engines that were “powerful, but very dirty.” Their project to reduce air pollution and to increase fuel efficiency of the two-stroke engines was sponsored by the Department of Science and Technology, Government of India, and later the concept was handed over to TVS India.
Another important contribution of the Department was developing cast-iron crankshafts – the rotating parts that form the backbone of an IC engine – to replace forged crankshafts in automobiles, which were expected to cut down production cost by 30-40%. S Seshan, Professor Emeritus and former Chair of the Department of Mechanical Engineering (ME), who has worked at IISc for 36 years, explains, “The crankshaft is a critical component of any automobile, and mandates premium properties. It is a fairly intricate steel component, and is complicated and expensive to manufacture. Ever since the advent of automobiles (such as the Ford models), crankshafts were invariably produced, all over the world, through the hot forging process. Our department ventured into developing ‘cast crankshafts’, with the aim of reducing the weight as well as the cost, without compromising on the property standards. The availability of ductile iron and Austempered ductile iron served as yet another incentive for such an endeavour.”
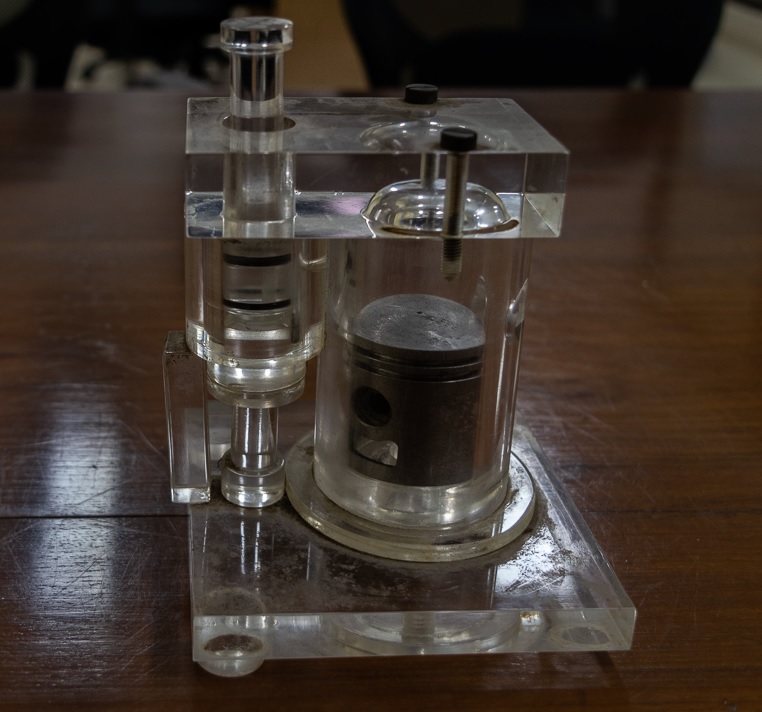
(Photo: Gouri Patil)
Manohar, in the ME Department’s Golden Jubilee souvenir, recalls a lab accident that turned into a fortuitous discovery. When an engine using the cast-iron crankshaft was being tested, a sudden power fluctuation made the engine race to “abnormal” speeds. But the crankshaft didn’t suffer any damage, proving that it was quite durable. “It was [re]assuring that cast crankshafts had gone through a test condition totally unanticipated.” These engines were later tested in taxis in Bombay and in vehicles plying on different terrains, he adds. “There was not even a single case of failure.” Despite the promise offered by cast-iron crankshafts, for reasons that are lost to time, they did not end up in commercial use.
Winding down
Although ICE and the Department of Mechanical Engineering merged much later in the 1970s, ICE seems to have struggled to acquire funding for several years before. As a 1953 brochure states, “It may be stressed however, that other countries are spending a far greater amount on similar work, and unless sufficient help is forthcoming, both from the Government and private enterprises, it may not be possible to solve the numerous problems connected with and arising from, the quest for an indigenous IC Engines Industry in India.”
The Annual Reports in the 1960s mention several collaborative projects between ICE and the ME section, until the merger. LS Srinath from IIT Kanpur’s Mechanical Engineering Department was put in charge of this merger by Satish Dhawan. J Srinivasan, a former faculty member at the ME Department, says that the merger was recommended by an international review committee that didn’t completely appreciate how rudimentary the Indian automobile industry was at that time. According to him, India still needed an academic department to study ICE. Seshan indicates that ICE was
comparatively smaller in size and hence the growth potential (in terms of the number of students and faculty, and lab facilities) became somewhat constrained. Plus, many aspects were common in the curricula and courses of the departments of ME and ICE. Added to this was the slow development of the Indian automobile industry and inadequate career challenges for IC engineers. All the above lead to the merger of the two departments, for more effective common academic activities.
But the transition wasn’t smooth. “That was a period of churn and change of direction,” says J Gururaja, former ME student and faculty member who later led the renewable energy programme at the Department of Science and Technology, Government of India. “Srinath wanted to shut down work on IC engines; he felt that the work of testing and certifying them for industry on the score that it also involved development research was nevertheless too “low-grade” for IISc, and that the Institute should focus its work on more fundamental research in newer areas.”
However, those turbulent times are long gone, and the ICE Department’s legacy lives on in the labs of current faculty members RV Ravikrishna, who studies combustion and flow dynamics and develops technology for using biofuels, and T Naik, who focuses on renewable energy, biofuels and emission control in IC engines. Himabandu M, a senior scientific officer, is also involved in developing alternative biofuels and thermoelectric generators for hybrid vehicles.
With input from Connect Staff and ME students
For more stories on the Department of Mechanical Engineering, please click on the links below:
Making Things Work: 75 Years of Mechanical Engineering
Remembering Arcot Ramachandran