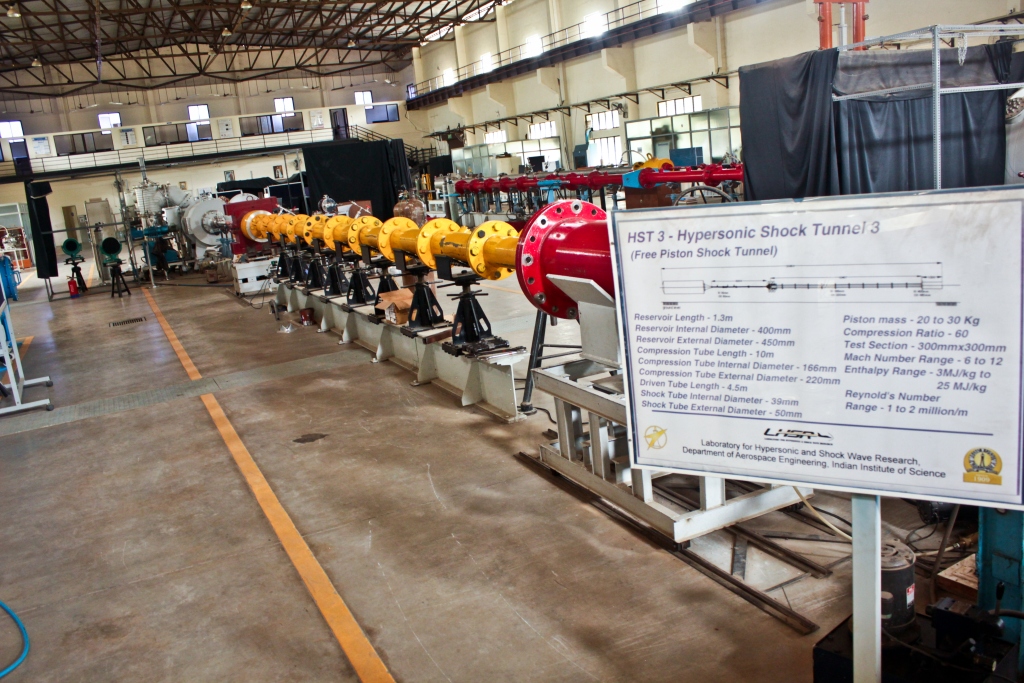
One of the largest shock tunnels in a university setup, India’s first hypersonic shock tunnel (HST) was built in 1973 at IISc by NM Reddy, who had studied under Irvine Israel Glass and Satish Dhawan. After holding several positions abroad, Reddy returned to India in 1970 and introduced shock tubes and shock tunnels in India for the first time, a facility which was extensively used for development or testing of ISRO launch vehicles, such as India’s first Satellite Launch Vehicle (SLV-3) and Polar Satellite Launch Vehicle (PSLV).
Until recently, shock tunnels were predominantly used by space scientists and aeronautical engineers to study heat transfer rates over space vehicles, such as re-entry vehicles, or components such as launch vehicle nose cones and bulbous heat shields. But today, the shock tunnel facility housed in the new Laboratory for Hypersonic and Shock Wave Research (LHSR) has five hypersonic shock tunnels, which are used for different purposes.
To learn more about the shock tunnels and how this facility has grown over the years, Connect spoke to Jagadeesh Gopalan (Professor, Department of Aerospace Engineering and Chairperson, Centre for Excellence in Hypersonics at IISc). Here are edited excerpts from the conversation:
IISc got its first hypersonic shock tunnel in the early 1970s. Could you trace its history and growth?
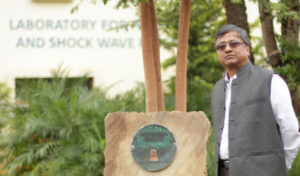
Professor NM Reddy had just returned to India, and started the High Enthalpy Aerodynamics Laboratory (HEAL) at IISc, which is now known as the Laboratory for Hypersonic and Shock Wave Research. In 1972, he built the first working shock tube consisting of a 32 mm diameter brass tube with a metallic diaphragm separating the driver and driven sections.
Subsequently, the country’s first hypersonic shock tunnel (HST1) was built in 1973, using an aluminium shock tube of 50 mm diameter with a conical nozzle and variable throats capable of producing Mach numbers in the range of 4 to 13.
To give a fair idea, during the 1960s and 70s, a shock tube was the only way by which high temperature, of the order of 4000 degree Kelvin, could be generated. It was around this time that India began its programme on Satellite Launch Vehicles (SLV) and Agni missiles. So a programme on shock tubes was started at IISc, as a requirement from the space community to measure the surface heat transfer rates in a typical launch vehicle nose cone and SLV model. But it was not enough to just look at heat transfer, and the space scientists wanted to see it in a real vehicle. Gradually, a nozzle was added at the end of the shock tube to create a Mach 6 flow, and that is how it became a shock tunnel.
How has the shock tunnel facility expanded since then?
At present, LHSR houses five hypersonic shock tunnels – Hypersonic Shock Tunnel (HST1), Hypersonic Shock Tunnel 2 (HST2), Free-Piston Driven Hypersonic Shock Tunnel 3 (HST3), Hypersonic Shock Tunnel 4 (HST4) and Combustion Driven Hypersonic Shock Tunnel (HST5) – all built for different purposes. HST2, made of stainless steel, was built to overcome the limitations on performance capabilities of HST1.
Subsequently, in the early 1990s, KPJ Reddy [Professor, Department of Aerospace Engineering] built India’s first free-piston driven hypersonic shock tunnel which can operate at very high enthalpy.
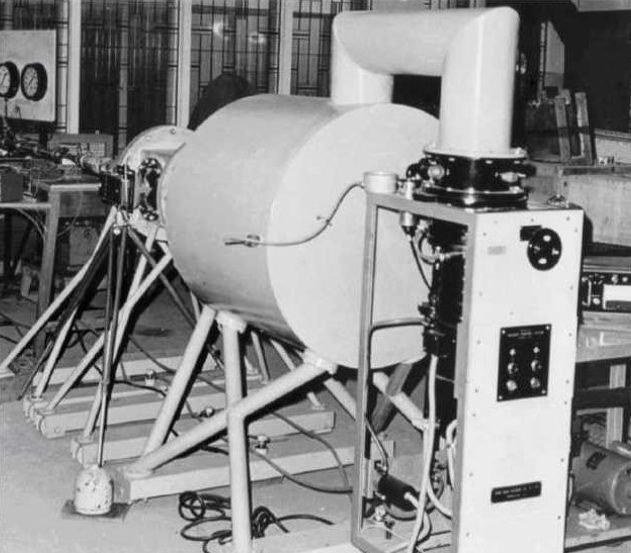
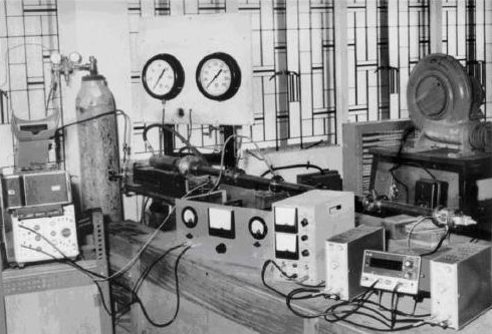
IISc is home to India’s first wind tunnel, an open-circuit wind tunnel, and also the hypersonic shock tunnel. How is a shock tunnel different from a wind tunnel?
A shock tunnel is an impulse facility which has the ability to produce high stagnation pressures and temperatures, with minimum power requirements and with reduced contaminant of test gas. Essentially, a shock tunnel is a short duration wind tunnel or an extension of a shock tube into a wind tunnel used in the experimental testing of aircraft, wing structures etc., and it is used to generate flows of hypersonic Mach numbers.
In a wind tunnel, the bodies of interest (test vehicles) are kept stationary; an air flow is created which has the same velocity with which the test vehicle is supposed to fly.
The major advantage of using a shock tunnel is that highly energetic flows of high stagnation enthalpy can be generated, which is required to study the features regarding flow around atmospheric re-entry vehicles, ballistic missiles etc. However, the most glaring disadvantage is that all tests have to be performed within milliseconds.
How are shockwaves formed?
Shockwaves are found not only around vehicles which travel at a speed faster than the speed of sound. When there is a massive energy dissipation which takes place in the shortest possible time, shockwaves can be formed naturally. It could be a nuclear explosion, an earthquake, a volcanic eruption, or a massive explosion in the outer galaxy when a new star is born. In fact, when the first nuclear explosion took place, they only saw the radius of the shockwave, which was hundreds of kilometres away. With the radius of the shockwave, we can actually work back and say what the energy [of the explosion] is.
History shows that apart from shock tunnels, there has also been work at IISc on shock tubes – Prof Satish Dhawan had been working on one. Could you talk about his research and how work on shock tubes progressed from there?
Dhawan was of course a visionary. Along with his former student NM Reddy [who was then working with CG Miller at NASA, and joined the Institute on Dhawan’s invitation], he built a small table-top shock tube. But it was not translated into a big shock tube where we can do meaningful measurements for industrial use, and it was not used to measure heat transfer. It was much later that NM Reddy happened to build the first shock tube, in which he was able to test the heat transfer rate on SLV.
Today, we have a hand-held shock tube called the Reddy Tube, named after its inventor Prof KPJ Reddy, which has applications in diverse areas like artificial insemination of cattle, investigating brain injuries due to accidents, removal of brain tumours, water purification, and oil extraction, among many others.
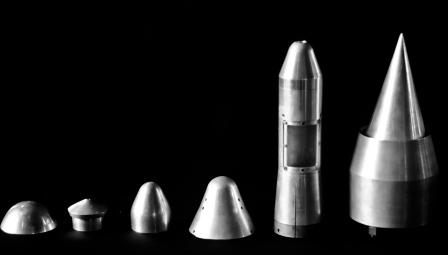
Considering that the facility started as a requirement for the space programme in India, what kind of research happens now?
What started out in this department 25 years ago was just for the space application. It was in 2001 that the shockwaves laboratory was established to understand what really happens when shockwaves travel through multiple media. Though numerous applications have sprung up using shockwaves, LHSR predominantly continues to work on aerospace-centric problems because such facilities are invariably required for very high military as well as space applications. But it would not be wrong to say that over the years, LHSR has also transformed into a hub of interdisciplinary research by bringing together materials scientists, chemists, biologists and industry people to solve many challenging problems in science.
For example, E Arunan [Professor, Inorganic and Physical Chemistry] uses shockwaves as a fundamental tool to understand high-temperature chemical kinetics, and has found out the minimum delay time for burning of jet fuel like JP-10 aviation fuel. This understanding is important because India is building what is called the scramjet engine, a supersonic jet engine.
Over the years, LHSR has transformed into a hub of interdisciplinary research by bringing together materials scientists, chemists, biologists and industry people to solve many challenging problems in science
Similarly, in collaboration with biologists, a first-of-its-kind experiment was conducted in which a micro-shockwave was used to put DNA inside a cell. This device has been patented. It has a few other applications, like putting preservatives in bamboo or removing bio-burden from a natural extract by killing bacteria.
Shockwaves are also finding application in managing chronic diseases. In diabetics, wounds take a long time to heal. A small hand-held device has been developed to reduce this healing time, which has been tested and is undergoing human trials.
In another collaboration with Dipshikha Chakravortty [Professor, Department of Microbiology and Cell Biology], India’s first, in fact the world’s first, needle-less drug delivery system has been developed.
What lies in the future?
India has not flown any air-breathing engine till now. Though ISRO did some experiments with hydrogen fuel a year back, there is no working system. So the next step is to build a hypersonic flight experiment where the engine development will be done by IISc.
The next step is to build a hypersonic flight experiment where the engine development will be done by IISc
One of our future goals is to build our own scramjet engine and do flight experiments so that India will join the bandwagon of select countries. The BRAHMOS-IISc Centre of Excellence in Hypersonics, to a large extent, will look at the fundamental technology and scientific issues associated with hypersonic flight.
Another jump for us would be the Centre’s new building which is expected to be ready before the Department’s 75th anniversary celebrations this year.