What goes on at IISc’s high-speed wind tunnel complex?
In 2015, an Italian tiltrotor military aircraft AW609 was on a test flight at high speeds and it crashed a few minutes after taking off, claiming the lives of both its pilots. Investigating the crash, the air-accident investigation agency ANSV pointed out that insufficient wind tunnel testing of the aircraft’s new tail configuration caused the accident. But what are wind tunnels and how do they ensure flight safety?
Wind tunnels are passages where the effects of high-speed air flowing past a scaled-down model of an object are studied. The object – be it a race car or bike, an aircraft, a missile, or even a flying dinosaur – experiences aerodynamic forces inside the wind tunnel, mimicking real world conditions. The data obtained from these tests help engineers improve designs, ensuring flight safety while also saving a great deal of money.
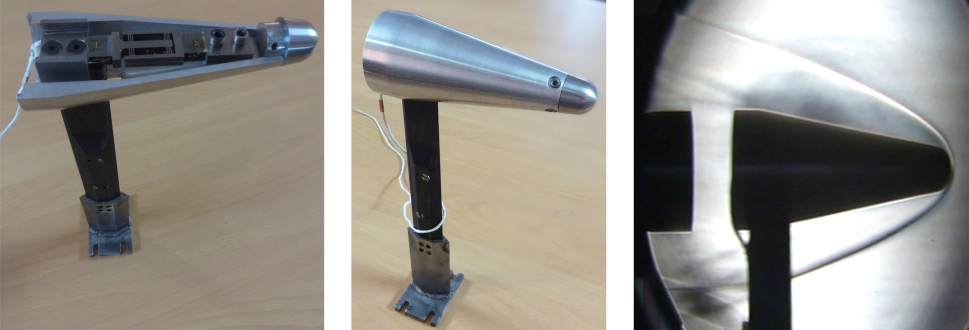
“We have to simulate conditions in a wind tunnel which must be geometrically similar to external conditions like total pressure, temperature, velocity, Reynolds number (ratio of inertial forces to viscous forces), Mach number (ratio of velocity of object to velocity of sound) and so on,” says B Vasudevan, Principal Research Scientist, Department of Aerospace Engineering, IISc. “Once these conditions are simulated, we perform tests to find out exactly what happens, for example, to a missile moving at high altitudes.”
Many missiles travel at supersonic speeds – that is, they travel at speeds ranging from one to five times the speed of sound, which is 344 metres per second at sea level. Hypersonic objects are those that travel even faster, at speeds as high as five to ten times the speed of sound.
To test objects moving at such high speeds, researchers use wind tunnels that can propel air to supersonic or hypersonic speeds. The first such facility in India was established at IISc in the 1950s in the form of the high-speed aerodynamics lab. “We [now] have three supersonic wind tunnels and two hypersonic wind tunnels,” Vasudevan.
“We [now] have three supersonic and two hypersonic wind tunnels”
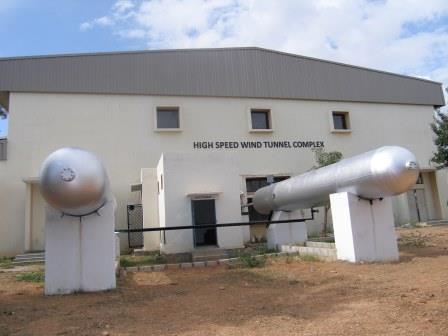
The work for India’s first hypersonic wind tunnel was begun in the early 1970s by Roddam Narasimha who was then a Professor at IISc, after obtaining a grant from the Government of India. Owing to a dearth of information on construction of hypersonic wind tunnels, as other countries with such facilities were hesitant to share details, the project faced hiccups. Nevertheless, Narasimha and team continued building the wind tunnel. “We were almost close to finishing it when Narasimha left IISc to become director of National Aerospace Laboratories (NAL). Before leaving he handed this part of the work to me,” Vasudevan recalls. After more than a year of relentless efforts, they installed a hypersonic wind tunnel with a diameter of 0.3 m in 1984 and in no time they bagged multiple projects. In 2012, Vasudevan and his group constructed another 0.5 m hypersonic wind tunnel.
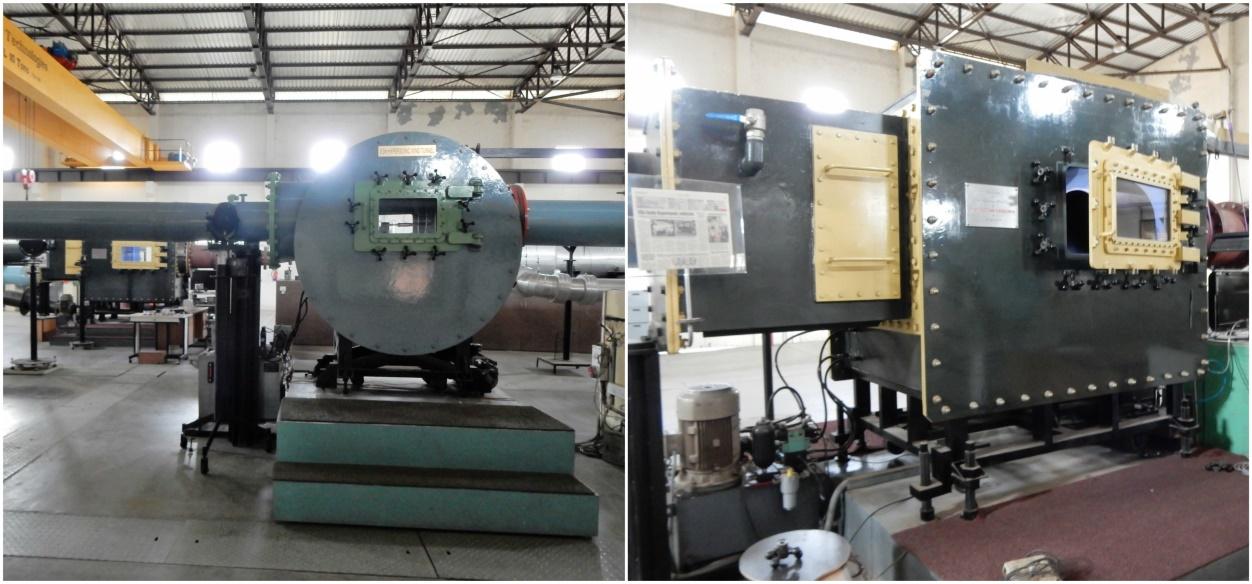
How wind tunnels help
Wind tunnel testing at hypersonic speeds is important because aerodynamic forces behave differently at such speeds and understanding them can prevent mishaps. Apart from the aerodynamic forces, motion at supersonic and hypersonic speeds cause shock waves that lead to a change in temperature, pressure, and density of air. As an example of an explosion caused due to shock waves, Vasudevan says that “a supersonic plane called SR71 that took off in 1966, exploded mid-air. They didn’t know shock waves can kill a vehicle.” This happens because shock waves can heat up structures, making them vulnerable to explosions. This can be avoided by using materials that can withstand high temperatures.
Travelling at speeds faster than sound poses another challenge – it can cause disruption in radio communication. Shock waves can dramatically increase temperatures in front of the plane, blocking radio transmission due to the formation of charged gas, also called plasma. Studying shock waves and its effects on models of an aircraft or a missile in a wind tunnel, therefore, is essential.
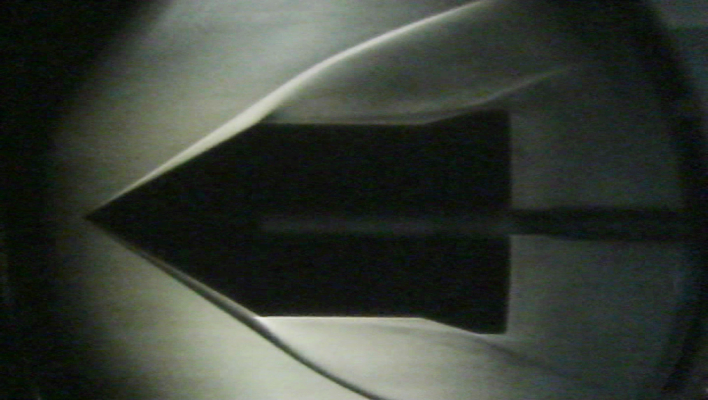
To evaluate the performance of a model, researchers use sophisticated instruments to obtain data, many of which have been developed indigenously at the lab. A strain gauge balance is one such instrument. “A strain gauge balance is a structural element which is fixed to the model being tested. Based on the proportion of the load [aerodynamic forces], it gives us an electrical output,” says Vasudevan. “There are only a few agencies in the world which have the capability to design and build such instruments. We design instruments for NAL and other defence centres. We have built instruments for Europeans and Canadians as well.”
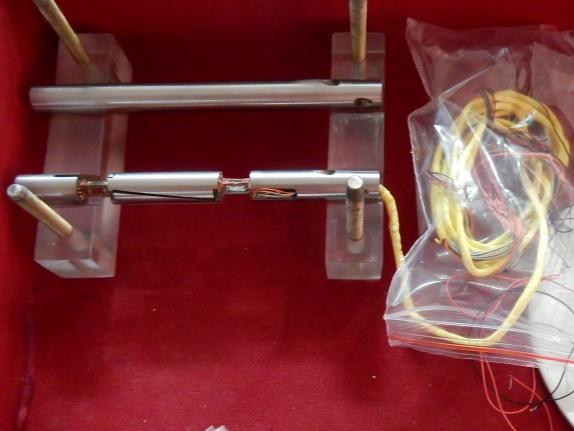
“There are only a few agencies in the world which have the capability to design and build such instruments. We also design instruments for NAL and other defence centres.”
IISc has taken a road less travelled by constructing instruments and wind tunnels from scratch. “We learned it the hard way,” says Vasudevan. “In this process, we have built over 100-150 instruments.” The instruments are constructed in-house and can cost more than Rs 1 crore, if imported. Currently, the facility boasts of having about 30 strain gauge balances. In addition to the strain gauge balances, the lab developed the first fibre optic wind tunnel balance to measure load, twenty years ago. “We were perhaps the first in the world to do that,” he says.
Although bigger wind tunnels give better results, lack of space on campus prevents the facility from expanding. The Chair of the Department of Aerospace Engineering, S Gopalakrishnan, says that the Government of India had expressed interest in setting up a hypersonic wind tunnel at IISc’s second campus in Challakere. “The wind tunnel, if approved, could have accommodated a model half the size of the Light Combat Aircraft,” he says. But this proposal didn’t materialise for various reasons. The government is on the lookout for other locations to set up a large hypersonic wind tunnel.
Collaborations
IISc has collaborated with both the Defence Research and Development Organisation (DRDO) and the Indian Space Research Organisation (ISRO). Vasudevan recalls that IISc set up its first hypersonic wind tunnel at roughly the same time that DRDO was developing its Agni missile. “Agni was in its early stages of development, and they [DRDO] wanted to get a lot of experimental design information and performance evaluation,” he says. The team has run perhaps 12,000-13,000 experiments for DRDO since then and the association with them stands strong even today.
“Agni was in its early stages of development, they [DRDO] wanted to get a lot of experimental design information and performance evaluation”
Through contractors, the high-speed wind tunnel complex team has worked with leading industry players too, like Honeywell, United Technology Corp, Airbus, and Boeing. The most recent project completed was for HCL Technologies. “They approached us as contractors for Airbus. We had to simulate rainstorm and sandstorm in our tunnel testing. This is important in places like Dubai,” Vasudevan says. He adds that they have completed over 100 scientific projects for industries and defence labs so far. The high-speed wind tunnel complex at IISc also provides services to other defence and industrial labs that do not have the facility.
What does the future hold?
The lion’s share of investment in hypersonic flight research goes into the military sector. India, too, is investing in the development of hypersonic missiles. Hypersonic passenger aircraft, meanwhile, may be possible one day, but given the fate of Concorde, which first flew in 1969 but stopped operations in 2003 due to difficulties recovering money and environmental issues, there are many hurdles to overcome.
In the recent past, the private sector has begun investing in hypersonic travel. For instance, in 2015, Airbus patented an idea for a hypersonic plane that could travel from Paris to Tokyo in three hours, a journey that today takes 12 hours. They are trying to develop, in collaboration with other countries, two other hypersonic vehicles that aim to travel at six times the speed of sound. Hypersonic wind tunnels will play a crucial role in developing such aircraft and ensuring their safety. Development of spacecrafts, too, will rely on wind tunnels to obtain data to model the launch, re-entry, and landing phases.
In recent years, computer simulations using computational fluid dynamics (CFD) has become a widely used tool for performance evaluation. However, says Gopalakrishnan, “for missiles and aircrafts, certification agencies need CFD and wind tunnel data to check for aerodynamic performance. CFD and wind tunnels cannot replace each other.” Wind tunnel testing, therefore, will continue to play an indispensable role in aerospace engineering.