Going beyond the ‘reuse, reduce, recycle’ model to curb plastic pollution
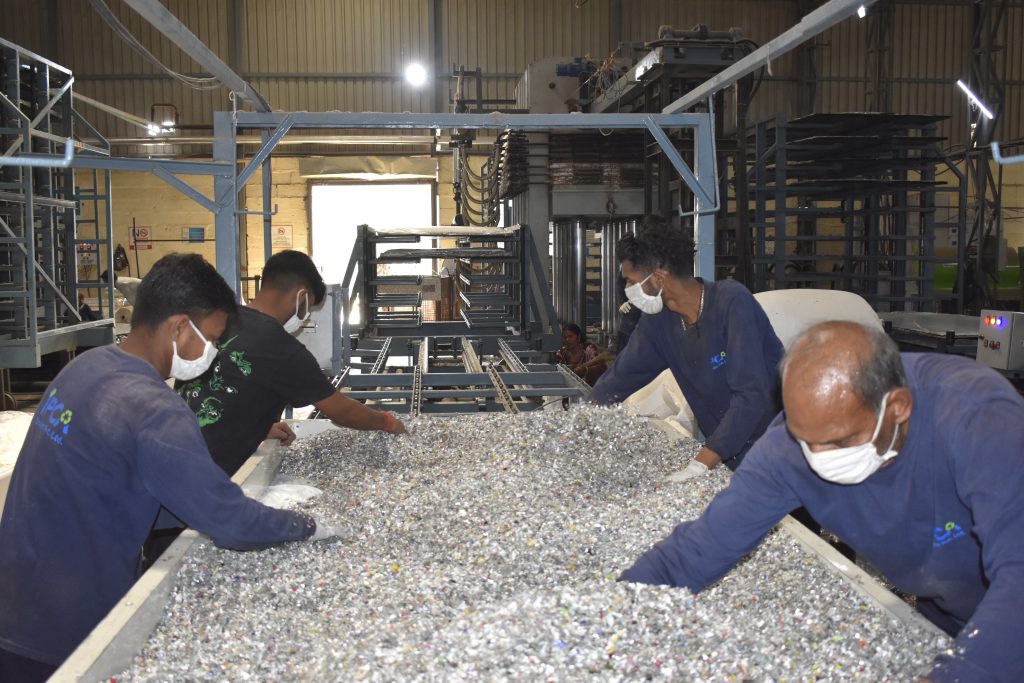
I turn off the alarm on my phone, slowly wake up, turn the fan switch off, and head to the bathroom. I push paste out of a tube onto my toothbrush, and brush my teeth. Then, I scoop water out of a peach-coloured bucket with a faded white mug to wash my face. Five minutes into the day and I’ve already touched six things made from plastic.
Throughout the rest of the day, I continue to note down anything plastic I touch, as science writer and author Susan Freinkel did for her book Plastic: A Toxic Love Story. While she recorded a whopping 196 plastic items in a single day, I could spot 60. My little experiment made me realise just how much plastic permeates our lives in various forms.
Our World in Data, an online open-access data platform, says that global plastic production reached a staggering 460 million tonnes in 2019, doubling in the last two decades. In India, every person produces 8 kg of plastic waste each year; although a small number compared to other countries, it is still significant considering the mountain of challenges associated with managing this material.
Plastic is heavily villainised these days, but it was once a much-needed invention. During the mid-1800s, elephants were killed for their ivory tusks which were then whittled down to make buttonhooks, piano keys, combs, and billiard balls. In 1863, a New York billiards supplier offered a handsome fortune to anyone who came up with an ivory alternative. John Wesley Hyatt, a 23-year-old printing press operator with a knack for invention, set up a shack behind his home and began experimenting. Five years later, he invented celluloid – a brittle substance created from plant cell walls (cellulose) that, while not hard enough for a billiards ball, had other uses like making combs, film strips and sunglasses.
Plastic is heavily villainised these days, but it was once a much-needed invention
The plastics boom began in 1907 when Leo Baekeland, a Belgian chemist, combined two chemicals – formaldehyde and phenol – under pressure, to create the first completely synthetic plastic, christened bakelite.
Over the years, several other plastics like nylon, teflon and polystyrene were invented. Plastics were cheap, durable and versatile compared to ivory tusks and tortoise shells. These properties made it easy to mass-produce telephones, radios, sunglasses, bullet-proof vests and so on. But today, these very perks have turned into perils. The same plastics that were created to prevent the exploitation of wildlife are now choking these creatures, finding their way into dense forests, deep oceans, and even human blood.
Plastic in labs
The invention of plastics was a boon for research as well. With single-use plastics, scientists working in labs did not have to worry about contamination as they could discard and use fresh equipment for their experiments. These practices continue to this day in many abs across the world, with only a few exceptions. But some scientists are also studying the impact of plastic waste generated in research.
“I’ve been doing research for almost 17 years, and we have been using plastics for a long time,” says Venkatesan Iyer, Facility in-charge of the Central Imaging and Flow Cytometry facility at the National Centre for Biological Sciences (NCBS), Bangalore. Around 2018, Venkatesan came across an article that estimated that five million tonnes of plastic were consumed in life science research each year. He was concerned that these plastics could not be recycled due to contamination with biological matter. “No company will try to segregate [this plastic],” he explains.
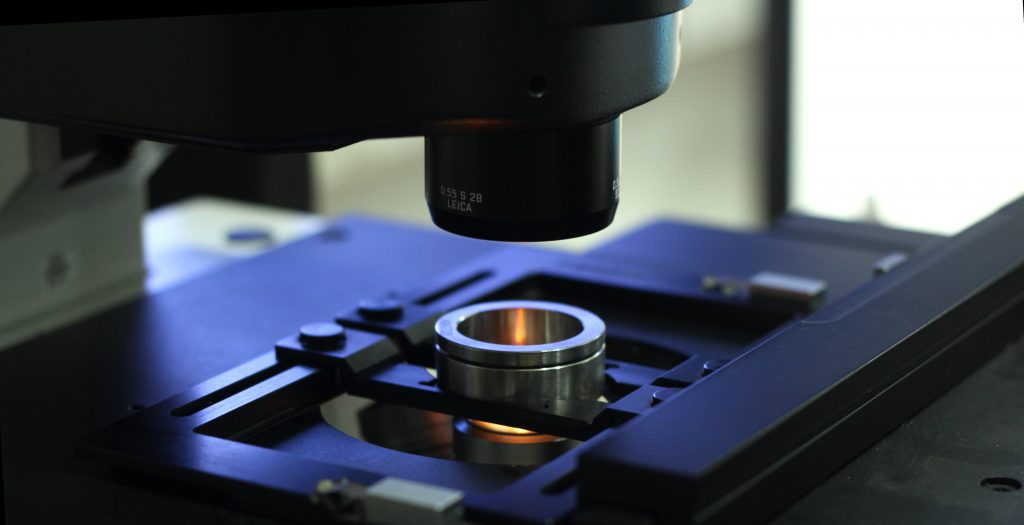
Venkatesan started looking for reusable alternatives. In 2022, he started a company called GreenFocus Research Technologies which develops GreenDish, a type of cell culture dish made from medical-grade stainless steel, the same material used by surgeons in bone grafts. He unscrews the top portion of the dish to show how cells can be placed inside with a cover glass on top and the entire set-up can be placed in a live-cell imaging microscope. Once the cell has been imaged, only the cover glass is discarded. The dish is washed and autoclaved in high-pressure steam making it sterile for its next use.
“The dish can be reused hundreds of times. Even if the material is discarded, it can be recycled completely,” says Venkatesan.
GreenDish is a reusable type of cell culture dish made from medical-grade stainless steel
In the same campus, about a hundred metres away, another scientist is looking at the problem from a different angle.
Kavyashree Manjunath’s interest had always been in the field of medicine and drug discovery. But after her PhD in crystallography at IISc, she joined a structural biology team at the Centre for Chemical Biology and Therapeutics (CCBT) at the Institute for Stem Cell Science and Regenerative Medicine (InStem), Bangalore. A multidisciplinary centre, CCBT carried out extensive cell biology and crystallographic studies, screening several lakhs of compounds regularly. But one aspect caught Kavya’s attention – the extent of plastic waste that was generated in the process. Though it seemed inevitable for any drug discovery lab, it made her wonder about the magnitude of plastic waste generated by science labs.
Kavya sifted through literature from the world of plastics to find some solution. She came across a study published in Science in which scientists discovered a bacteria in a recycling site in Japan that could “eat” polyethylene terephthalate (PET) polymers, and subsequently grow on PET waste. “I never thought there could be an enzyme which can degrade plastic,” she says. Until then, the research had largely presented only mechanical and chemical/thermal recycling solutions to plastic waste.

Combining this newfound knowledge with her protein engineering expertise, Kavya heads a start-up called Apratima Biosolutions incubated at the Centre for Cellular and Molecular Platforms (C-CAMP), Bangalore. Its focus is on developing enzyme-based solutions to recycle PET plastics that are used in packaging foods and beverages, especially small-sized soft drinks, juice and water. One of their enzymes can break down almost 90% of PET in just 17 hours. The byproducts of this process, terephthalic acid (TPA) and ethylene glycol, can be purified and eventually used as raw materials to re-manufacture PET.
One of their enzymes can break down almost 5 gm of PET in just 17 hours
Using enzymes to degrade plastic is still nascent, says Kavya, with only a handful of companies working on it around the world, like Carbios in France, Protein Evolution in USA, and Samsara Eco in Australia. There are several challenges that these companies need to overcome. One is the varying degrees of crystallinity of PET waste. Crystalline PETs are opaque and rigid while amorphous PETs are clear and flexible. But these forms interchange depending on the temperature. The enzymes used currently cannot access the crystalline structures of PET in order to break them down. Another issue, Kavya points out, is finding ways to reduce the amount of enzyme required to depolymerise PET. Thirdly, the enzyme is not reusable. Separating the enzyme from the byproducts is an expensive process.
Once the pilot studies are approved, Kavya plans to partner with industries that can produce the enzyme in larger quantities and then take this technology to recycling industries. “It can be integrated with existing mechanical recycling industries,” she says.
The recycling conundrum
Most people believe that if they put plastic waste in a particular bin, it will get recycled, says Kavya. “We never think about what actually happens beyond that point.” The truth is that it is difficult to find out how much of discarded plastic reaches the recycling centres and how much ends up in landfills or oceans. According to a 2023 report by the Commonwealth Scientific and Industrial Research Organisation (CSIRO), only about 8% of plastic consumed in India is recycled.
Aditya Kabra, founder and CEO of a greentech startup called ZeroPlast Labs, says that while plastic consumption is one problem, lack of waste segregation is another. “If we mix food waste with plastics or other recyclable things, it becomes extremely difficult to remove the recyclable material,” he explains. Organic waste also generates methane when it reaches landfills, giving rise to more carbon emissions. “Once we have full scale waste management facilities along with segregation and proper regulations, I think we can reach up to 80-90% of recycling rates, especially for plastics,” he says.
According to Deepanshi Gandherva, Assistant Manager, Communications, at the Indian Pollution Control Association (IPCA), as part of the Extended Producers Responsibility (EPR) guidelines that come under the 2016 Plastic Waste Management Rules, the Central Pollution Control Board (CPCB) mandated that producers, importers and brand owners (PIBOs) should develop a system to collect the plastic back from the environment. “But there was no clear action plan for the environmentally-sound collection of plastic waste,” Deepanshi explains. So, in 2017, IPCA – a non-governmental organisation (NGO) – prepared and executed an EPR action plan starting with five brands, namely Pepsi, Dabur, Perfetti Van Melle, Dharampal Satyapal Ltd, and Nestle. Today, Deepanshi says that they work with more than 200 PIBOs to execute these EPR guidelines.
Only about 8% of plastic consumed in India is recycled
Several states like Maharashtra, Karnataka and Tamil Nadu have issued mandates to plastic manufacturing industries to stop the import, manufacture, sale and use of single-use plastics like polystyrene and expanded polystyrene. Government initiatives like Meendum manjappai, which promote using yellow cloth bags instead of single-use plastic bags, also show promise.
Even though the country is moving in the right direction regulation-wise, Kabra is concerned that hasty inventions of plastic alternatives may cause other problems. For example, many companies have started using plates made from bagasse (the dry pulpy fibrous material that remains after crushing sugarcane). But these contain a layer on top made of PFAS, a carcinogenic substance that is banned in Europe and the USA, but not in India.
A recent study, published in the journal Environmental Science and Technology, also revealed that plastic products have lower greenhouse gas emissions compared to their alternatives in 15 out of 16 applications, such as producing grocery bags, food packaging, milk containers, wet pet food containers, and so on. “What good is a shift away from plastic bags if the paper alternative emits more GHG emissions across the product life cycle?” the authors write.
“This haphazard shift towards alternative materials without studying the implications is where we are creating more harm to humans and the environment,” Kabra adds.
The truth behind bioplastics
During his Bachelor’s studies at the Indian Institute of Science Education and Research (IISER), Pune, Kabra used to go on plastic pick-up drives once every two months, and was appalled by the enormity of plastic items he’d encounter every time.
He thought of developing a material that could decompose just like an orange or banana peel. Soon after, he met Kadhiravan Shanmuganathan, a scientist at the CSIR-National Chemical Laboratory, who wanted to commercialise a biopolymer developed in his lab. The two started ZeroPlast Labs in 2019. The company developed compostable bioplastics using cellulose from crop residues – reducing waste for farmers as well as providing an alternative to virgin plastic.
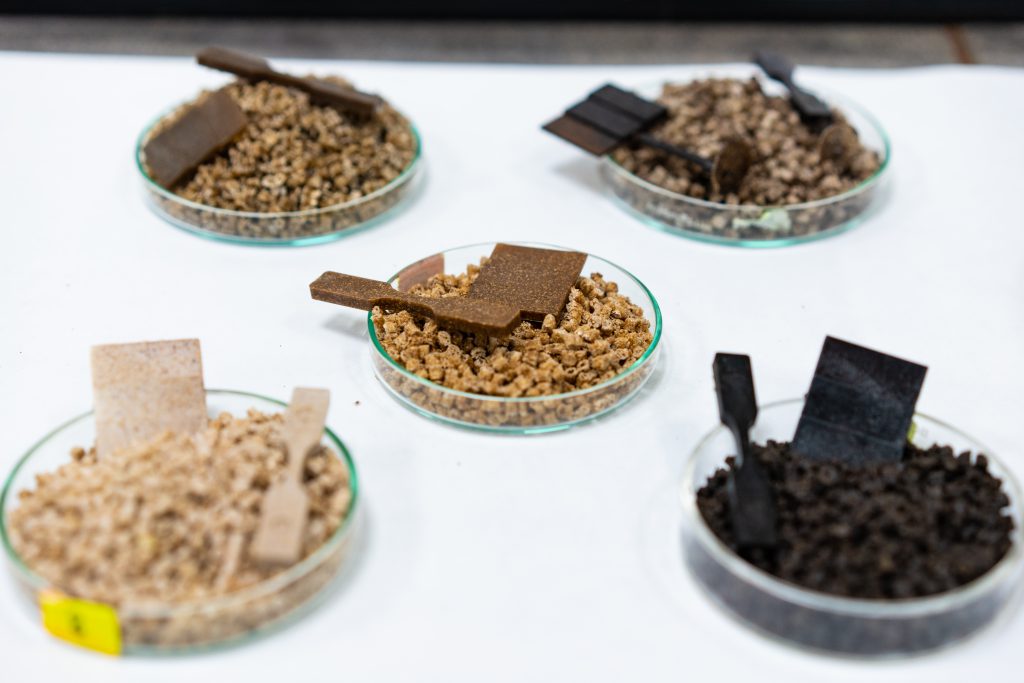
Five years later, the company has now paused its operations. One reason, Kabra says, is that the carbon footprint is equivalent to oil-based plastics. This includes the energy used for developing raw materials which, in the case of bioplastics, includes fertilisers, land and water for the crops. “We don’t see any benefit in using biobased or biodegradable materials over virgin plastics – the environmental impact is the same,” he says.
Bioplastics are also less resistant to moisture, and so cannot be used like conventional plastics for protecting food. “There is a trade-off between barrier properties and compostability,” Kabra says.
Another reason is that biodegradable or compostable plastics do not degrade naturally like fruit and vegetable peels. “Bioplastics require industrial composting facilities to degrade,” Kabra says. There are no such facilities in the country that maintain the right moisture, temperature and environmental conditions for these bioplastics to break down fully. Eventually, they end up in landfills, lasting for hundreds of years, making them no better than oil-based plastics.
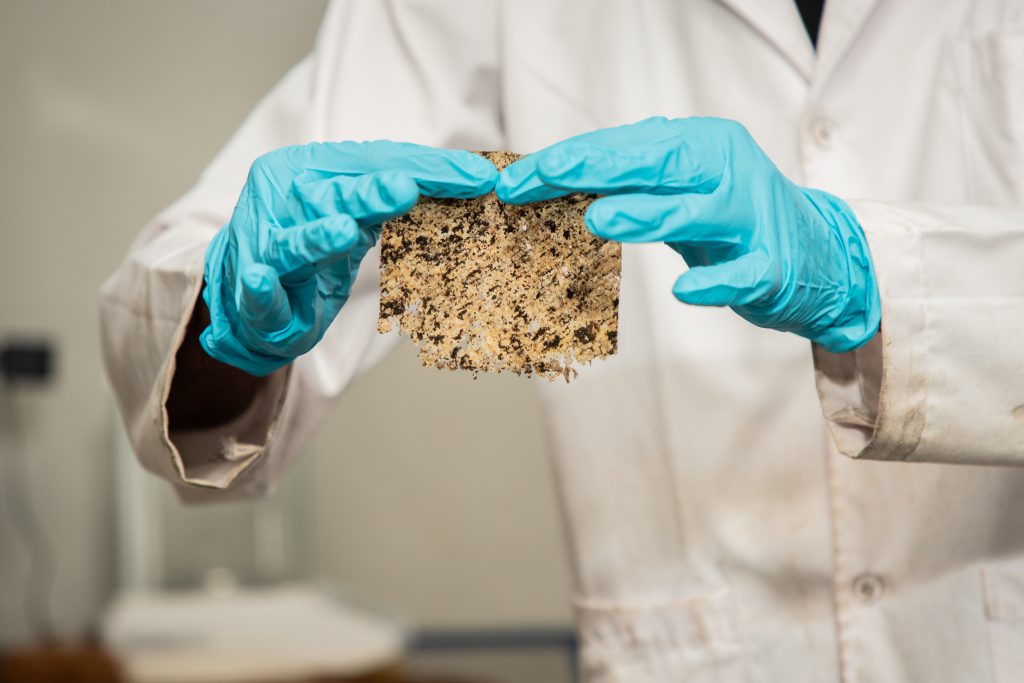
Towards a circular future
Plastics are not evil on their own. They do not leach into the environment, says Suryasarathi Bose, Professor at the Department of Materials Engineering, IISc. “But when it is not disposed of properly and subjected to environmental conditions, that’s where the problem begins,” he says. His lab focuses on designing new bioplastics that can be degraded without requiring industrial facilities, and finding ways to transform discarded plastics.
Using precursors from oils and cellulose from crop stubble, Suryasarathi’s lab and collaborators have developed bioplastics, similar to Kabra’s ZeroPlast Labs. But, according to Suryasarathi, these degrade completely without affecting the environment – they do not leach out harmful chemicals when buried under the ground.
When it comes to plastics, one of the most challenging types is the multi-layered plastics or MLPs. These have at least one layer of plastic with another layer made of aluminium, metal films, polymeric materials or paper. Supply chains for collecting and recycling this type of plastic did not exist as they were difficult to integrate into the collection system, says Deepanshi. Therefore, IPCA set up two units for recycling MLPs where they recycle over 900 metric tonnes of plastic waste in a month to develop chipboards – similar to plywood but resistant to termites, water and fire – that can be used to build utilitarian products.
Similarly, Suryasarathi is associated with VOiLA3D, a startup that collects MLPs and moulds them into useful products like furniture or pots. These can further be recycled so that they fit into the circular economy, he says. The concept of circular economy is designed around reusing or refurbishing materials as long as possible instead of the ‘take-make-waste’ linear model.
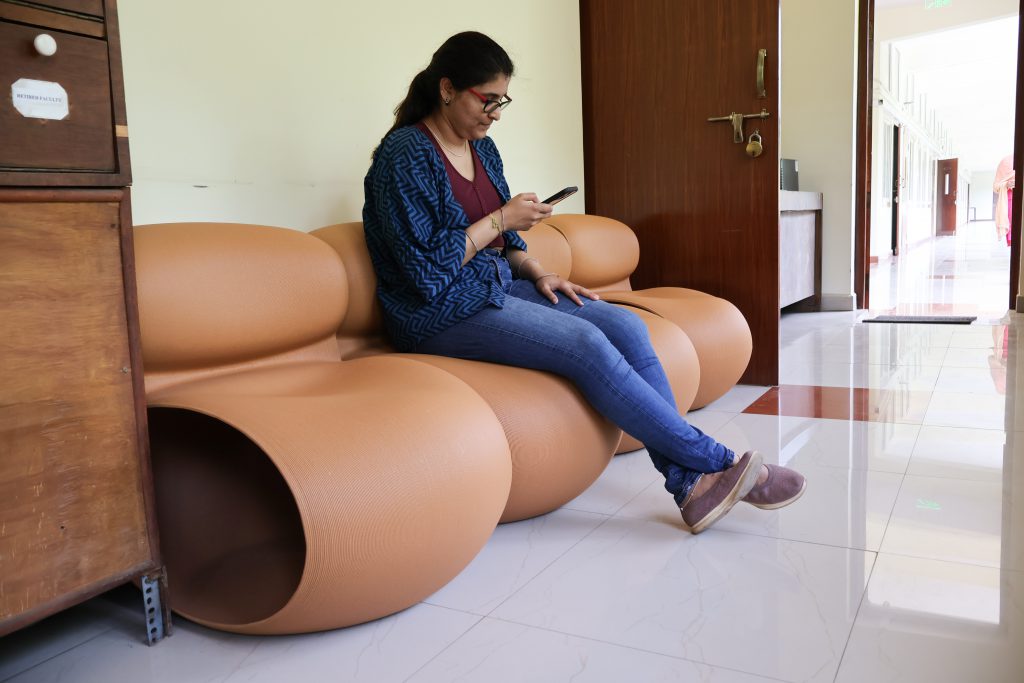
Suryasarathi adds that government support is important for creating awareness and bringing in policies. “For example, if there are kiosks made for returning all our shampoo bottles and oil containers, it is easier for a recycling plant to pick it up.” As of now, NGOs like IPCA run several community engagement programmes to bring about behavioural changes in society towards segregating waste, zero littering and recycling.
While there are plenty of technologies and solutions being innovated, individuals can segregate waste to ensure it gets recycled for reducing plastic waste generation, says Kabra.
Beyond the three R’s of recycling – reuse, reduce, recycle – we should add another ‘R’ called refuse, Venkatesan suggests. This can start with something as simple as refusing tea or coffee given in paper cups – which are usually coated with a thin layer of plastic – and asking for steel or glass cups which can be washed and reused.
As I was writing this article, I chanced upon the comprehensive waste recycling manual published by the Bruhat Bengaluru Mahanagara Palike (BBMP) that describes how to sort organic and plastic waste. While I cannot do much about the plastic that permeates my life, I can start by rinsing off my next milk packet or ice cream wrapper before throwing it in the dustbin, and carrying a trusty steel tumbler whenever I step out to the IISc canteen for my usual cup of chai.