India is betting big on lithium-ion batteries, but at what cost?
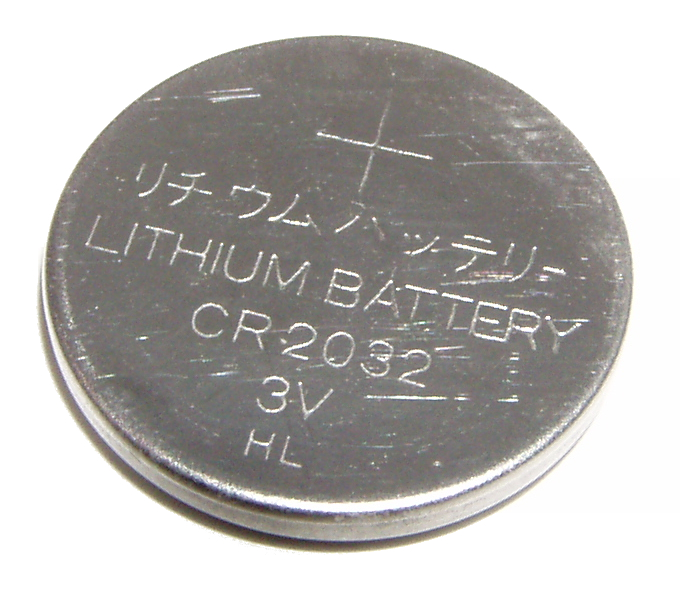
In 1817, Johan August Arfwedson, a Swedish lawyer and mineralogist, was studying the mineral petalite in the laboratory of the renowned chemist Jacob Berzelius. His investigations revealed that the mineral mainly contained aluminium, silicon and oxygen. But around 4% of the composition could not be accounted for. Arfwedson also noticed that this missing part was chemically similar to sodium, potassium and other alkali metals. Confused with this result, he exposed the petalite sample to a flame, and the flame immediately turned carmine red, a colour never seen before in any flame test. Surprised by its chemical behaviour, Arfwedson named this newly discovered metal “lithium”, derived from “lithos”, the Greek word for stone.
The discovery of lithium went largely unnoticed until an Australian psychiatrist named John Cade started experimenting with this metal for treating bipolar patients during World War II. In 1950, he, along with colleagues Mogens Schou and Poul Baastrup, showed that a controlled dose of lithium could reduce the symptoms of bipolar disorder. This generated a sudden excitement for lithium. In the following years, chemists also began looking at its energy-storing capabilities, and companies started making batteries utilising this metal.
Lithium – often referred to as “white gold” – is a much more precious resource than fossil fuels. Only 22 million metric tonnes of lithium reserves are presently available worldwide, whereas, in 2020, the world’s total oil reserves was estimated to be 236.29 billion tonnes. Most of the mineral is confined to the so-called Lithium Triangle – Bolivia, Argentina and Chile – which has more than 75% of the world’s lithium reserves. Countries like India have, therefore, been importing lithium for decades.
“Lithium – often referred to as “white gold” – is a much more precious resource than fossil fuels”
But in 1996-97, India too struck gold, metaphorically. The Geological Survey of India (GSI) discovered the presence of large lithium reserves in Jammu and Kashmir. However, there were no serious attempts to explore them. Twenty-six years later, in 2023, the Ministry of Mines finally announced the presence of about 5.9 million metric tonnes of “inferred” lithium reserves in the same place in Reasi district. This was just two years after GSI reported the presence of around 1,000 metric tonnes of lithium reserves in the Mandya district of Karnataka.
Even though scientists and activists are worried about the environmental impact of mining such reserves, industries, especially those working on electric vehicles and energy storage technologies, are excited. And for good reason. If the Ministry’s estimates are validated, then the net worth of the Reasi reserves alone can be as high as Rs 34 lakh crore, substantially cutting down India’s spending on importing lithium, which was about Rs 9,000 crore in 2022. This may just be the tip of the iceberg, given the massive craze for transitioning to clean energy. And it certainly has a lot to do with the fact that lithium has now become the poster boy of the battery industry.
From clay pots to cellphones
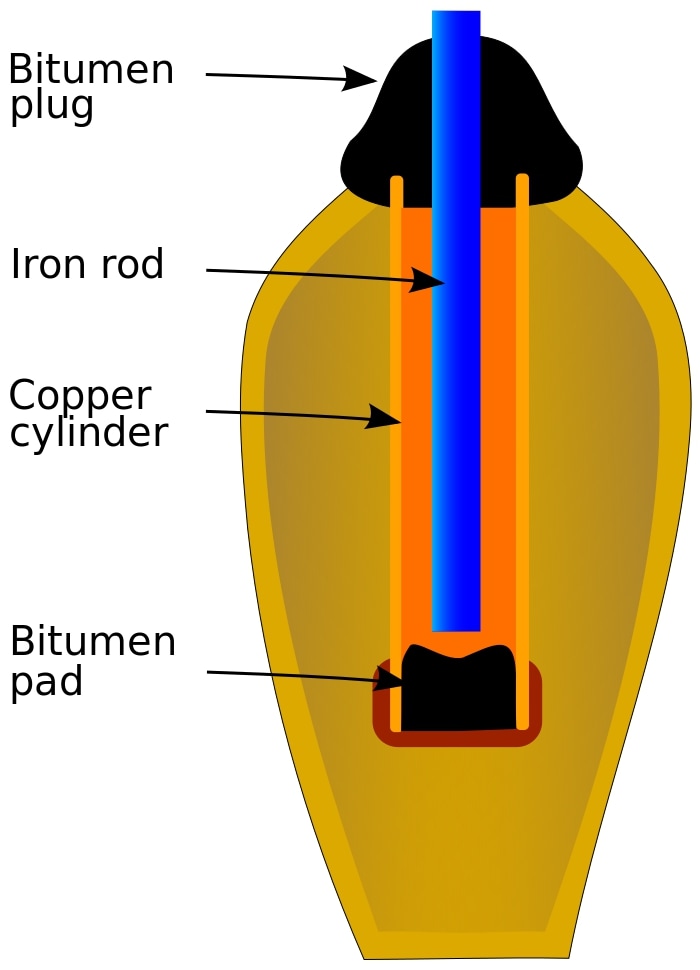
In 1936, a German archaeologist named Wilhelm Konig was excavating a 2,000-year-old village called Khujut Rabu near modern-day Baghdad. During the excavation, he came across an unusual 5 inch-tall clay pot, which encapsulated a copper cylinder and had an iron rod suspended in the centre of the cylinder. The cylinder and the rod did not touch each other and were separated by an asphalt plug. Konig concluded that the pot belonged to the Parthian dynasty (from around 250 BCE) and that its structure resembled a very primitive form of electrical battery. Konig named the pot “the Baghdad battery” – the earliest battery known to humans.
In today’s world, batteries play a crucial role in our lives. From the heavy lead-acid batteries used in buses and trucks to the tiny dry cells used to switch on our laser pointers, we have come up with several innovations in battery technology. As the world marches towards greener forms of energy, scientists believe that batteries are critical to the transition from non-renewable energy sources to renewable ones. “[Energy from] renewables is intermittently available; hence, it must be stored. At present, batteries are the most preferred choice for energy storage because they are modular, scalable and easily transportable,” says Naga Phani Aetukuri, Assistant Professor in the Solid State and Structural Chemistry Unit (SSCU), IISc. “Right now, there is sufficient reason to switch to renewables. However, this is limited by the availability of batteries with the necessary techno-economic attributes. The good news is that this transition to renewables plus batteries is inevitable in the years to come.”
The cost of production of energy from renewable sources like solar panels and wind turbines has gone down significantly in the past decade, but the need for storing renewable energy in batteries forces the net cost to increase by three to four times of that spent for generating power from coal, according to Naga Phani. Recent advances in lithium (Li) ion technology could enable the shift to green energy sources while still being economically viable.“Batteries today are consumables, and the one parameter that the consumer cares about the most is cost. The cost of ownership is expected to be much lower for lithium-ion batteries than any other battery in the market today,” adds Naga Phani. “Cheaper batteries also mean lower costs for green electricity.”
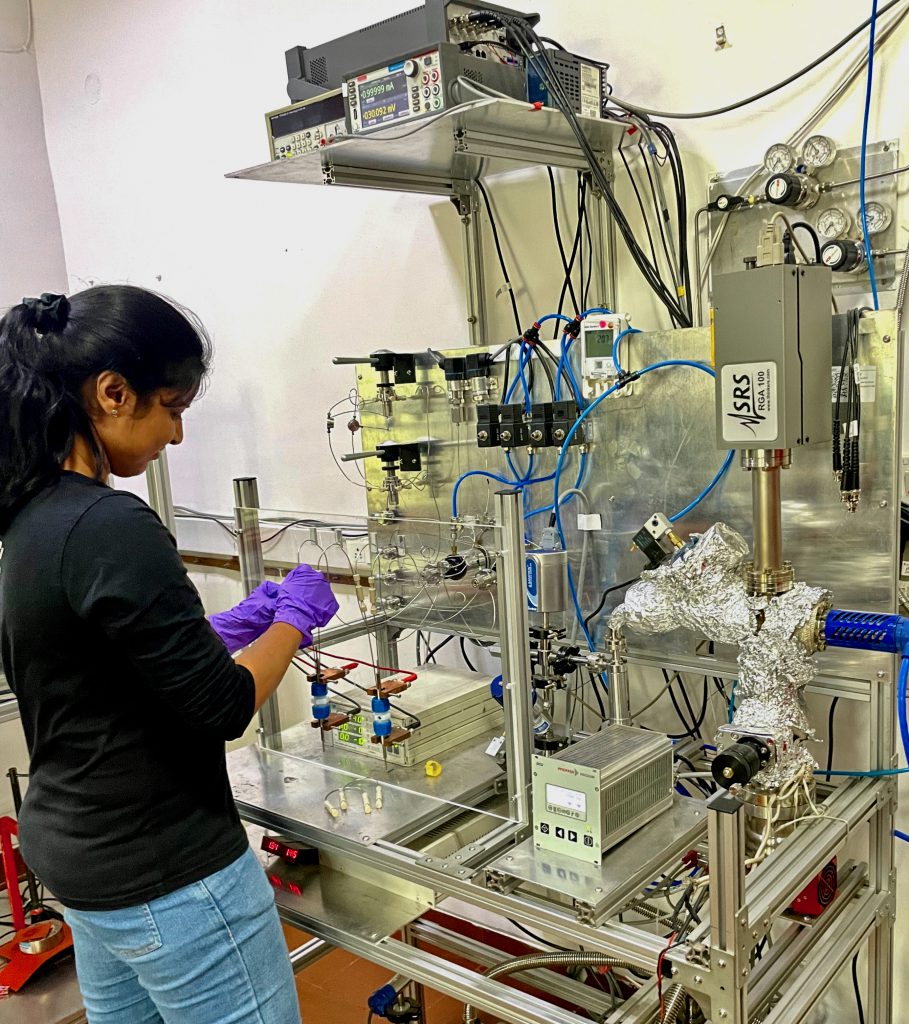
Akhila S from Naga Phani Aetukuri’s lab setting up batteries on a differential electrochemical mass spectrometer (Photo courtesy: Naga Phani Aetukuri)
Today, Li-ion batteries are used abundantly in automobiles, mobile phones, laptops and other electronic devices. Compared to other types, these batteries last much longer and have a higher energy density – which means more energy storage while using a tiny amount of lithium. “Li-ion battery has made great strides. In 1991, a Li-ion module cost around USD 1,000 with a power output of 90 kWh, whereas today, the energy output has gone up to around 250 kWh with the cost coming down to less than USD 100,” says Aninda Jiban Bhattacharyya, Professor in SSCU and the Interdisciplinary Centre for Energy Research, IISc.
This enormous increase in cost-efficiency has a lot to do with the evolution of the chemical composition of the Li-ion battery over the years. And this change began just three decades back.
Mining, manufacturing and mass production
In 1985, a Japanese multinational company called Asahi Chemicals, led by scientist Akira Yoshino filed a patent demonstrating the first safely rechargeable Li-ion battery. This sparked a massive interest among companies like Sony and Panasonic, which were aiming to commercialise Li-ion batteries. Keizaburo Tozawa, the then Chairman of Sony Corporation, was excited about the prospects of this novel technology, but at that time, his company lacked the recipe to produce these batteries on a large scale.
Five years later, Sony took a giant step in the memory storage sector – shifting from tape recorders and cassettes to CDs (compact disks). During this transformation, Tozawa was visiting a company manufacturing unit and happened to come across the tape-recorder assembling equipment lying idle, waiting to be discarded. He had a sudden epiphany – the manufacturing process of these tape recorders and cassettes involved sprinkling a polymeric foil with magnetic nanoparticles. Tozawa immediately realised that the same technique could be used to coat Li-ion powders or inks onto metallic films and assemble Li-ion battery modules on a large scale. This procedure is still being followed for making Li-ion batteries, exclaims Naga Phani.
In 1991, Sony brought out the CCD-TR1 8 mm camcorder powered by commercialised Li-ion batteries, becoming the first company in the world to do so. And Yoshino, along with two other scientists, was awarded the Nobel Prize in Chemistry in 2019 for the development of Li-ion batteries.
The 1991 prototype had a graphite anode (negatively charged electrode) and a transition metal oxide-based cathode (positively charged electrode). Today, state-of-the-art Li-ion batteries available in the market primarily consist of cathodes made of lithium cobalt oxide or lithium iron phosphate. The most commonly used cathode consists of cobalt oxide, but it is costly and toxic. Therefore, researchers are working on finding a proper replacement for cobalt. “India is largely betting on lithium iron phosphate-based cathodes because they tend to be a lot safer to use. Continuous usage of a battery with lithium iron phosphate does not cause the electrolyte to heat up significantly, rendering the battery very stable even at temperatures as high as the average summer temperature in India. But there is a compromise – this has a lower energy density than the cobalt-based ones,” says Naga Phani.
A major problem with conventional batteries, in general, is that continuous usage leads to a strong heating effect, known as a thermal breakaway reaction, which can even result in an explosion. Li-ion batteries also use liquid electrolytes that are highly reactive and have low flash points (flash point is the lowest temperature at which the electrolyte starts combusting), which can also cause the battery to explode. In addition, these batteries have a non-conducting and polymer-based separator between the positive and negative electrodes, which reduces the battery’s efficiency.
“‘The transition to renewables plus batteries is inevitable in the years to come'”
Ongoing research in Naga Phani’s lab aims to make Li-ion batteries safer and more compact by replacing the polymeric separator and liquid electrolyte with a solid-state electrolyte. To keep the battery light, the researchers have successfully replaced the carbonaceous anodes with solid-state lithium metal-based ones. These changes are expected to increase the energy density of the batteries by 30-40%. This could significantly lower the battery cost, thereby enabling the widespread adoption of batteries for green electricity.
Aninda’s group works on both Li-ion and beyond Li-ion chemistries. Over the years, the focus of their research has been to design alternative Li-storing anodes and Li-ion conducting soft matter (“solid-like”) electrolytes (cross-linked polymers, gels and viscous liquids). They have also proposed and designed carbonaceous materials like 2D (doped) graphene, nanostructures of transition metal oxides, sulphides, and tin alloys as alternatives to graphite. Their goal is to assemble Li-ion batteries with electrodes developed in-house along with multi-functional soft matter electrolytes. All these efforts are expected to lead to a more energy-efficient and cost-effective Li-ion battery module.
But the cost-effectiveness also depends on how much we must spend on getting raw lithium. In theory, the extraction of lithium is a straightforward process. In South America’s Lithium Triangle, for example, lithium is extracted from brine, a highly concentrated salt solution of lithium found in underground reservoirs or seawater. The brine solution is stored in evaporation tanks, and the lithium concentration of the brine is carefully monitored as the water evaporates. This gives an estimate of the amount of lithium that can be extracted from the brine solution. Adding sodium carbonate to the brine solution yields lithium carbonate, from which metallic lithium can be directly obtained and used in batteries.
But Aninda believes that the Reasi reserves might be present in the form of mineral ores, like spodumene and petalite. In that case, the mineral needs to be taken through a protocol of processes comprising crushing, roasting at very high temperatures (around 12000 °C) and acid leaching. “This entire process of lithium extraction from ores is cost- and energy-intensive (vis-a-vis extraction from liquid brine), demands heavy machinery, and the yield may still be low,” says Aninda. “India does have the necessary infrastructure to mine and extract lithium, irrespective of the starting material; however, certain industry-compatible optimisations might need to be adopted.”
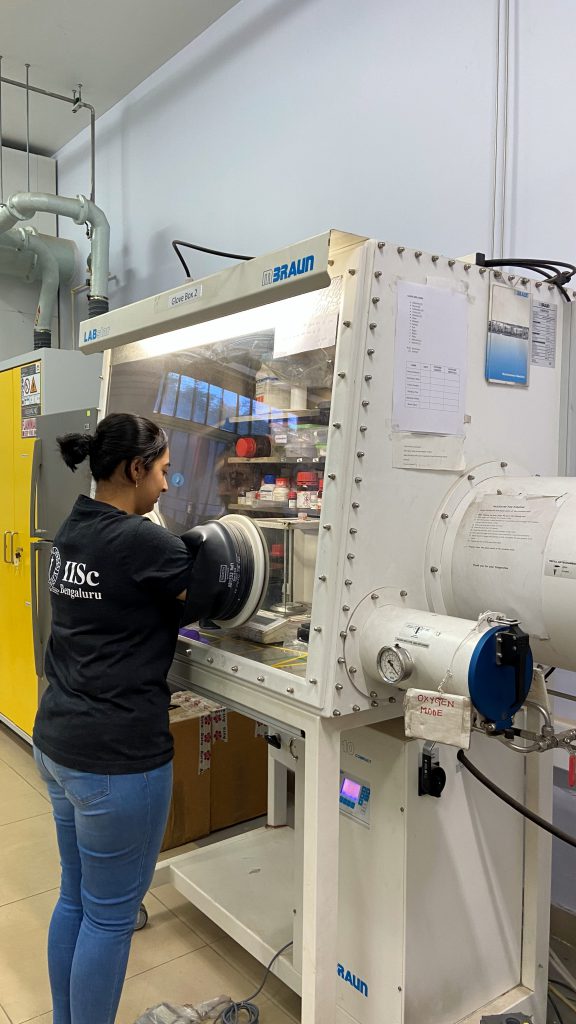
Impact on ecosystems
While industry and government sources gear up to capitalise on the Reasi discovery, the presence of the reserves has also stirred up a socio-political and environmental storm. The area where the lithium reserves have been identified has large plots of agricultural land and a dense forest cover. The Chenab river also flows quite close by. Lithium mining can therefore pose a serious threat to these natural resources.
“[Mining] creates fragmentation in the forest habitat and hampers the movement of animals residing in that area,” says Rajkamal Goswami, Fellow in Residence at the Ashoka Trust for Research in Ecology and the Environment (ATREE). He adds that mobilising and deploying heavy mining machinery and infrastructure can alter the landscape rapidly, which, in turn, can severely impact flora and fauna.
Rajkamal explains that among the most affected would be small creatures such as worms, spiders, snails and frogs. These animals do not move much in search of food or mates. Consequently, mining-related excavation can completely wipe out their populations.
Incessant dumping of chemical waste into the water can affect and kill fish. During the limestone mining boom in Meghalaya in 2007, Rajkamal recounts how a 4 km-long stretch of the Lukha river downstream from the mining site had “literally no fishes.” Birds and large mammals can travel large distances from the mining site. But this territorial displacement can cause drastic shifts in the ecosystem.
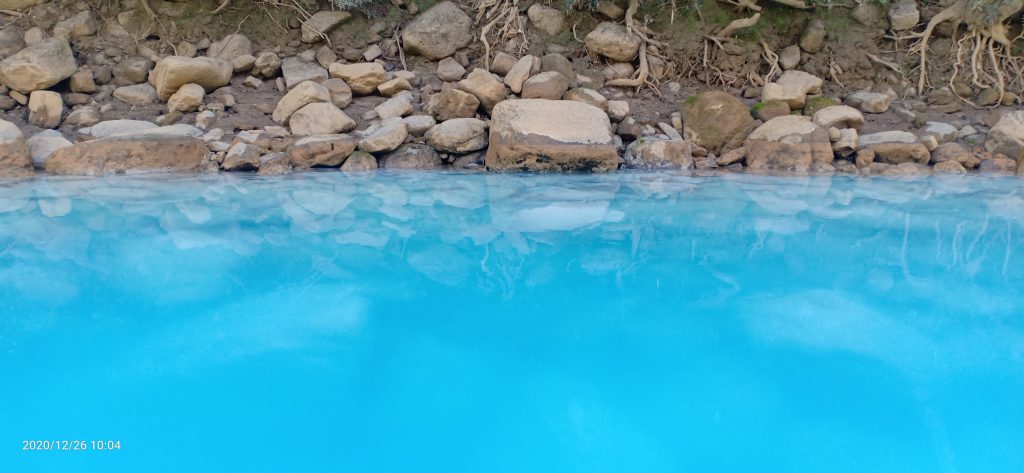
“Before 2007 [when the cement and limestone mining began], the forest cover in this region was much more than what it is now,” says a local official who works in a government organisation in Sonapyrdi, Meghalaya. “The Lukha river was the most affected – all the aquatic life in the river has vanished over the last 15 years.” Because of the large number of pollutants dumped into the river, the water has turned deep blue due to the excessive growth of toxic blue-green algae.
However, there are ways to minimise the mining-related damage to the ecosystem. For example, mining can be done across one small patch of land at a time, then shifting to another small patch, and so on – just like cultivating small tracts of land – instead of mining over a large area all at once. This allows the patch of land that has been mined some time to recover. “In developed countries, they plan the development of industries and infrastructure in such a way that they keep the resilience of the ecosystem in mind and phase out the extent of any possible disturbance to the level that it doesn’t affect the ecosystem critically,” adds Rajkamal.
Every ecosystem has a threshold for the disturbance it can tolerate before collapsing or changing irreversibly. He believes that for the Reasi reserves, the authorities should similarly try to understand the natural systems and find the threshold. “If you are planning to dump lithium-associated waste into the water bodies, find the optimum dumping rate beyond which it will negatively alter the aquatic ecosystem balance. Beyond that rate, you will simply destroy the water body,” says Rajkamal.
“There are ways to minimise the mining-related damage to the ecosystem”
Large-scale unplanned mining can also disrupt the lives of the local villagers who depend on the forest and the local water bodies for their livelihoods. In some areas, many private land-owners are happy to sell their land to the government or industries for mining, especially when the land is not agriculture-friendly. But in most areas, like Meghalaya, for instance, local villages and communities have been cultivating common land for many years. Therefore, when limestone mining began in 2007, large scale appropriation of common land took place for excavation, and left the poor and marginal farming communities destitute and vulnerable.
“Unless there are strong policies in place for environment conservation, it will be difficult for the common man to save the planet through individual or collective action alone,” says Rajkamal.
Engaging and interacting with local communities, who might be directly affected by the mining at Reasi, even before the operations are planned, will also go a long way to ensure the mining is carried out safely and sustainably. But Rajkamal is sceptical. “Given how scarce lithium is,” he says wryly, “I don’t think these companies will allow any delay or obstruction to the immediate procurement of the mineral.”
Aniket Majumdar is an Integrated PhD student in the Department of Physics, IISc and a former science writing intern at the Office of Communications