In 2011, the Indian Institute of Science (IISc) signed an MoU with BrahMos Aerospace to create a new centre for studying an exciting aspect of scientific research in today’s world: hypersonic flight. The Centre of Excellence for Hypersonics was inaugurated that year by APJ Abdul Kalam, former President of India and eminent aerospace scientist.
Although research on hypersonics has been conducted in India for the last few decades (particularly at IISc – India’s first hypersonic shock tunnel was built here in 1973), there had previously been no major dedicated programmes, says Jagadeesh Gopalan, Professor at IISc’s Department of Aerospace Engineering and Chairperson of the Centre. “The Centre came together in 2011 because of Dr Kalam, Prof N Balakrishnan [then IISc’s Associate Director], Prof P Balaram [then IISc’s Director], and Dr A Sivathanu Pillai [Founder-CEO and Managing Director of BrahMos Aerospace],” he says.
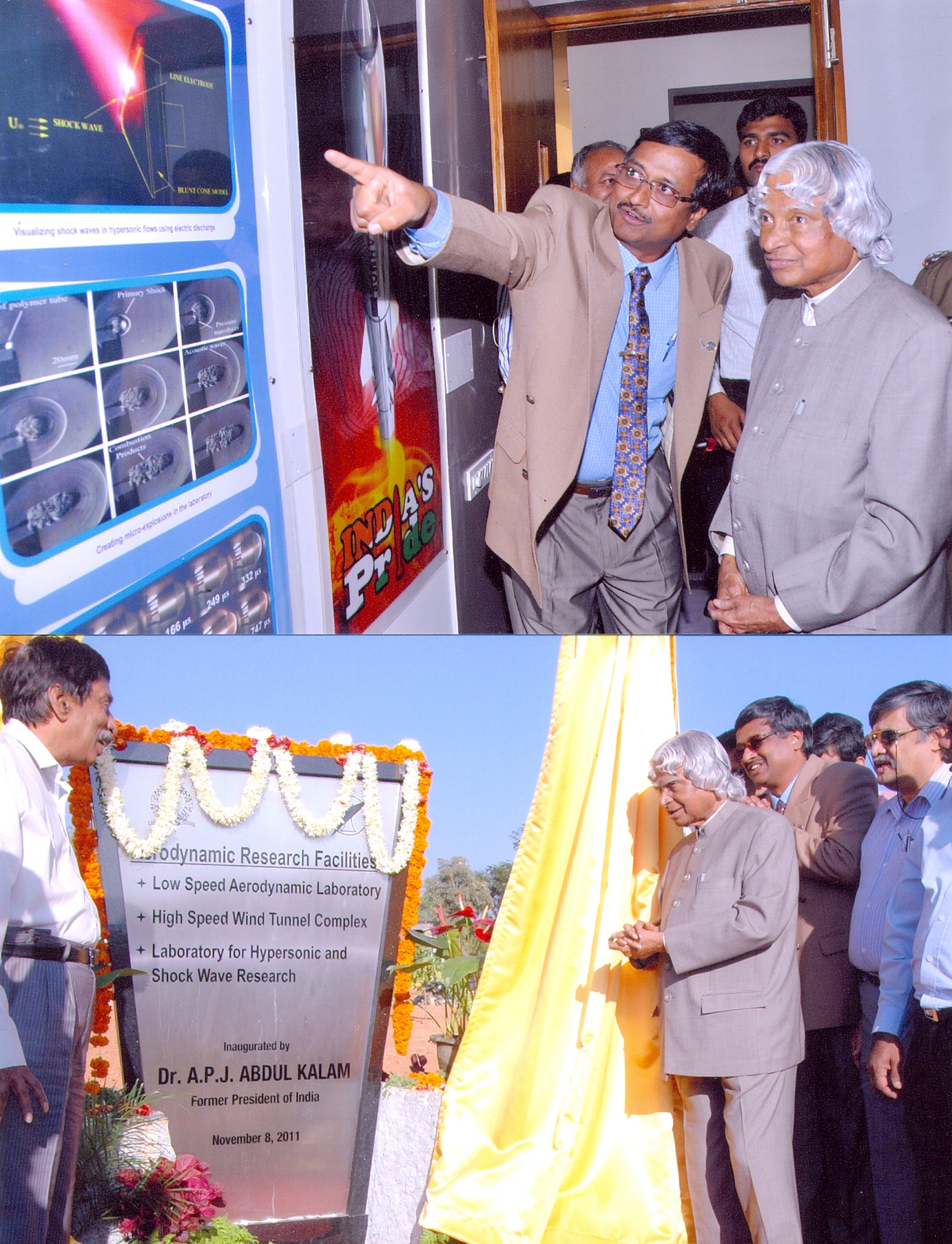
“We were very clear that there would be no missile development here – our focus would be fundamental science, engineering and technology issues in the broad area of hypersonics research,” he adds. The Centre, a separate entity located in the Department of Aerospace Engineering, follows a unique model – young BrahMos scientists are posted here full time, working alongside IISc’s faculty and students across multiple departments. Gopalan describes the vision for the Centre as being to complete the “jigsaw puzzle” of hypersonics research, which necessarily combines work from different disciplines. The existing Laboratory for Hypersonic and Shockwave Research (LHSR) at IISc was itself formed in 2010 combining multiple existing laboratories under the Aerospace Department involved in highly interdisciplinary work from materials research to chemical kinetics, and lends much of its expertise to the Centre.
Since it was opened, the Centre has worked successfully on projects worth Rs 35 crore, says Gopalan. He adds that the Centre gives IISc the opportunity to work with industry (which IISc encourages through its faculty entrepreneurship program – Gopalan himself is the co-founder of a private company), while helping scientists at BrahMos build on their “intellectual capital” through fundamental research on hypersonic flight.
What is hypersonic flight?
The flight of an object can be said to be hypersonic if it occurs at speeds five or six times that of sound or above Mach 5 (sound travels at a speed of 330 m/s. Flight is said to be supersonic if it is faster than the speed of sound). Missiles such as Inter-Continental Ballistic Missiles (ICBMs) and space shuttles can travel at hypersonic speeds, particularly while re-entering Earth’s atmosphere. This is associated with high drag and heat transfer, and surface body temperatures can rise up to 6,000 Kelvin. And because the hypersonic regime is dominated by such a large amount of kinetic energy, the atmosphere around such vehicles in flight itself is dissociated – the air breaks down into oxygen and other smaller particles.
Cracking these aspects of hypersonic flight involves incredibly complicated physics that few have managed, but its implications are enormous. For one, as Gopalan points out, “This area is very fertile from an experimental as well strategic point of view for the entire world. It can enhance the capability of the country in terms of deterrent technologies which are required for geopolitical strategies.” A hypersonic arms race is currently on, with Russia, China and the US being the main competitors. Missiles travelling at such speeds would be difficult to intercept, and in mid-2017, Russia tested Zircon, its “unstoppable” hypersonic missile system that it claims could make US missile defense systems obsolete. Around the same time, Boeing announced it was planning hypersonic jets in the next two decades for commercial flights that could take premium passengers from New York to Shanghai in two hours.
The ‘flying laboratory’
Recreating the conditions around hypersonic flight in order to study them in a laboratory is an enormous challenge. “IISc has made a phenomenal contribution in solving non-linear partial differential equations, right from the days of satellite launch vehicles [made by ISRO], computational fluid dynamics exercises in which Dr Kalam was involved right here, right from the time he worked at DRDO,” says Gopalan. He adds that it still isn’t sufficient to paint an accurate picture with theoretical studies. “Because the atmosphere around the vehicle is dissociated, it is not easily amenable to mathematical treatment.”
It is therefore important to experimentally test hypersonic flow. IISc’s wind tunnels and shock tunnel facilities can help recreate hypersonic flow conditions in the laboratory. “You keep the body stationary but create an air flow that has the same kind of characteristics as outer space. Because energies are very high, you cannot recreate these for a very long time – just a few seconds. For really high energies like in shockwave research, experimental times are even lesser, like one millisecond,” Gopalan points out. The ideal way to conduct hypersonic research would be to have a “flying laboratory”, he says, where flight tests could be carried out in order to improve on design. “It might require many flight tests to get info about fundamental physics, like laminar to turbulent flow transitions, which is an important parameter. In India, we have not even begun to do hypersonic flight tests as a mechanism to understand design data. One of the big challenges I have been facing is to start that culture,” he adds.
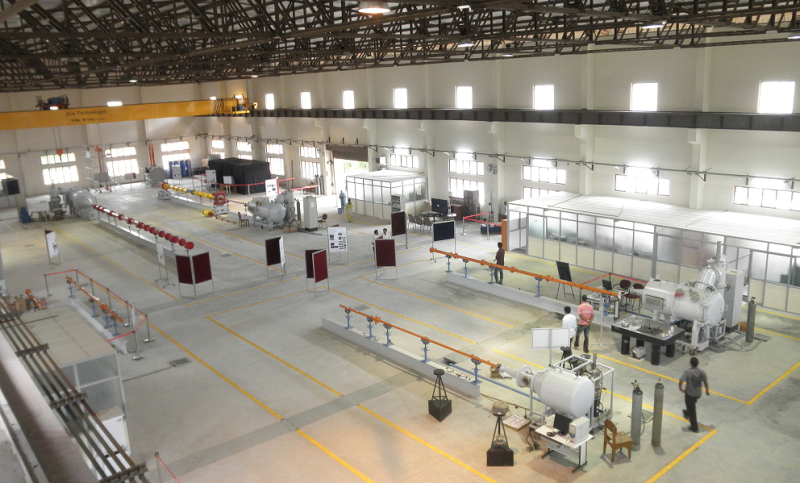
“For example if I generate Mach 6 flight [in a wind tunnel] on a generic blunt body which will resemble a flight vehicle, and I get surface heating rates on which I base my design, how good is that data? [I won’t know] unless I do a flight test and it survives in actual flight. For us, this is an excellent and exciting opportunity as scientists to be able to do actual experiments so that we can take our numerical data to the next level,” says Gopalan.
Solving the jigsaw puzzle
The hard part – and the exciting part – about working on hypersonics is that the approach to it “can’t be segmented”, as Gopalan puts it. Every aspect of how a vehicle that travels at hypersonic speed is designed has to be integrated. For one, there’s the material used to build the external structure of the vehicle. As it needs to withstand extremely high temperatures, it cannot be made of metal. Ceramic appears to be the best candidate, and work on high-temperature ceramics is being done in collaboration with Bikramjit Basu, Professor at the Materials Research Centre – one of several instances of how the Centre of Excellence collaborates with students and faculty across disciplines at IISc.
The coating on the surface of a hypersonic vehicle should not make it a catalytic surface – at high temperature, an endothermic reaction (one that absorbs energy) would drive the surface temperature even higher. “We had done some very exotic work many years ago on using this phenomenon itself to create an exothermic reaction, so that the shockwave can be pushed away from the vehicle’s surface,” says Gopalan. Currently, a group led by D Roy Mahapatra, Associate Professor at the Department of Aerospace Engineering, is working on these high-temperature-resistant thermal coatings.
Hypersonics is dominated by a phenomenon called shockwave, which moves faster than the speed of sound and exerts drag force on the vehicle that it forms around. The region between the body and the wave exists at a very high temperature. Being able to calculate the distance between the body and the wave would help understand how much thermal protection the body would need.
Simply capturing a shockwave on film was a big deal at IISc in the mid-90s, amidst pioneering work on shockwaves, according to Gopalan. Taking a photograph that would show what a shockwave looked like was a big project, based on a challenge from Kalam. “Prof KPJ Reddy and his team built the first free piston shock tunnel in India, and only about seven countries in the world have such capability,” he says.
Another piece of the jigsaw puzzle is aerodynamic design. The wing cross section has to be unique, with a thickness of 1 mm at the leading edge, gradually increasing to 18 mm further. The front portion of the vehicle therefore requires additional lift, and shockwaves can be utilised to provide this. Such design is known as the “waverider”. Prof N Balakrishnan at the Department of Aerospace Engineering is working on computational modeling of some of the aerodynamic aspects of such intricate shapes, using computational fluid dynamics (CFD) code called HiFUN, developed indigenously. The waveriders were also tested by the hypersonic wind tunnel team led by Vasudevan, with computations and experiments going hand-in-hand.
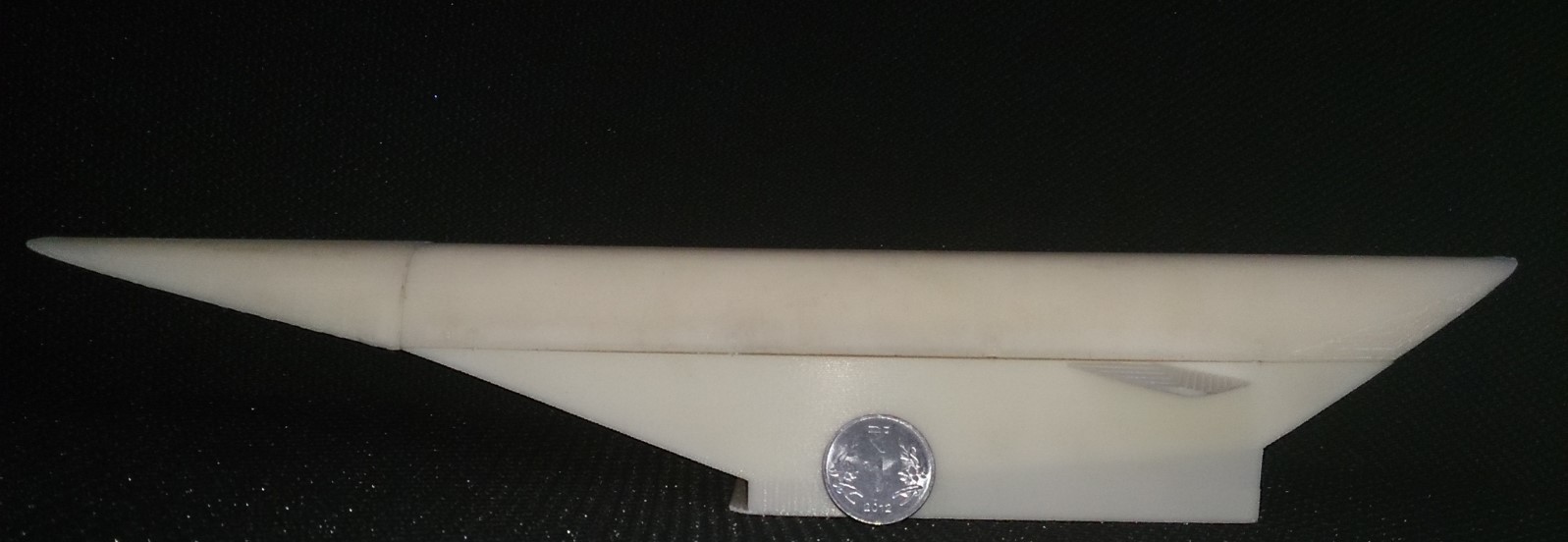
Designs require state-of-the-art Multi-Design Optimisation (MDO) tools, and SN Omkar, Chief Research Scientist, and his team are working on advanced MDO tools that can be combined with other computational tools to gain further insights into the hypersonic vehicle design process.
A simultaneous activity at the Centre is the effort to build a supersonic combustion ramjet engine, better known as a scramjet engine. A scramjet engine uses the shock reflection and the high temperature generated behind it to burn fuel using oxygen present in the air, rather than oxygen carried in a tank. This makes the aircraft lighter. The design of a scramjet engine is unusual to say the least – it looks like a long, narrow, hollow duct, and has no rotating parts. Fuel injected into the engine burns as it goes along and the hot gases produced as a result expand into the engine’s diverging cross section, generating the required thrust. A scramjet testing facility was recently built on campus by Swetaprovo Chaudhuri, Assistant Professor at the Department of Aerospace Engineering and his team, right from scratch, and will soon be commissioned. “This is the first such facility in a university in the country where advanced laser flow diagnostics will be integrated to probe the fascinating regimes of combustion of fuels at supersonic speeds,” says Gopalan.
Then there’s the question of the chemical reactions within the engine, work on which is carried out by KPJ Reddy, Professor at the Department of Aerospace Engineering, in collaboration with E Arunan, Professor at the Department of Inorganic and Physical Chemistry. A shock tube is used to understand high temperature chemical kinetics – research on it has been going on at IISc since the late 90s. “What is the chemical kinetics associated with such fuel? How do you ensure auto ignition – that it burns immediately – in a very short time? How do you ensure it burns completely?” These are the questions they’re working to address, says Gopalan.
Guidance and control of the vehicle is another tricky part of their research, aided by Ashwini Ratnoo, Assistant Professor at the Department of Aerospace Engineering. Given the incredibly high speeds at which the vehicle must travel, creating software that updates fast enough to track the vehicle’s path and guide it pose a challenge. And the vehicle’s sensors need to be able to function at very high temperatures, for which the Centre plans to work with IISc’s Department of Electrical Communication Engineering and the Centre for Nano Science and Engineering.
Young scientists
Helping piece together this puzzle at the Centre are eight young scientists with an average age of 27, recruited by BrahMos after completing a BTech or MTech and stationed at IISc. Ragini Mukherjee, who works on structures, Priyamvada KS, who works on guidance and control, and Manoj Kumar K, who works on computational fluid dynamics methodology for hypersonic flows, are among those who work at the Centre full-time, under the guidance of faculty members and in collaboration with other students across departments.
They are in the unusual position of working for industry while being embedded in an academic environment. “We are getting the right training, knowledge and experience here at this age, which we can carry with us wherever we go from here,” says Nimesh Thakor, one of the scientists from BrahMos. It isn’t quite the same as working towards a PhD at IISc, as their responsibilities don’t just lie towards the Centre. “Let me put it this way,” says Thakor. “During a PhD you have only one boss. Right now, I have three bosses to answer to,” he says while his colleagues chuckle. “Our research has to be application-oriented,” says Mukherjee, “in a PhD, the academic research you do may not always have that goal.”
Gopalan describes the Centre as a “win-win collaboration”. It has helped the Institute augment its hypersonic research facilities, such as the new direct connect mode scramjet test facility, small material testing facilities, and is now a hub where ME students have started using tools built for design. At the same time, for Gopalan, the intellectual pursuit remains in the forefront. A new wing is currently under construction and is scheduled to be inaugurated in November, ahead of the Department’s platinum jubilee celebrations later this year.