3D printing is revolutionising manufacturing
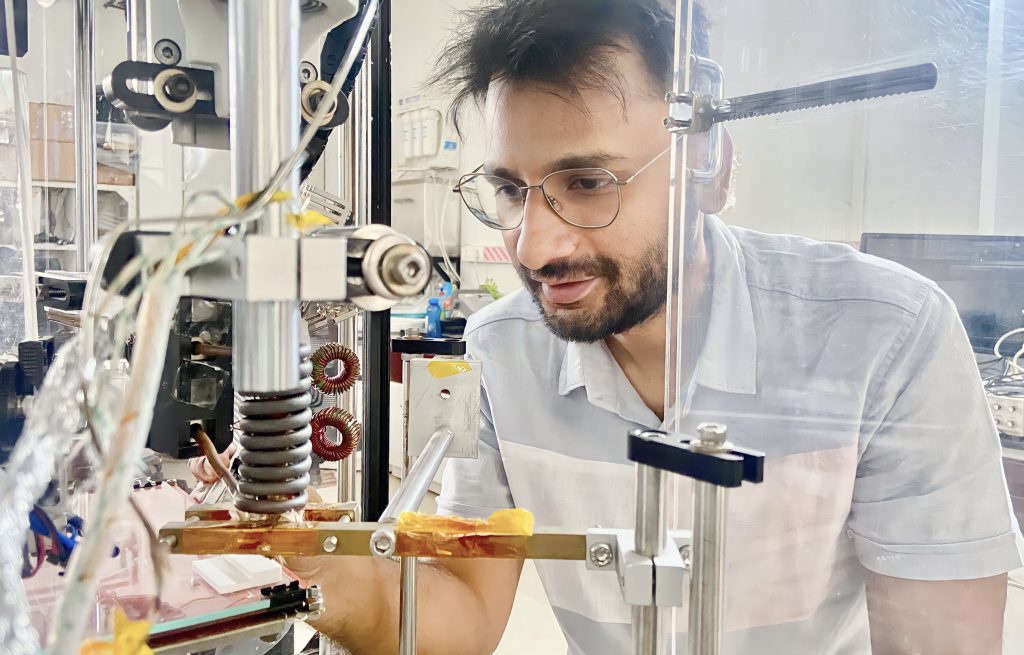
(Photo: Arun Kumar)
As a young kid, Shashank HR was fascinated by how things, including his toys, were made. So, he would be thrilled whenever he had a chance to visit his father’s metal fabrication shop, where he witnessed how sheets and rods of steel were shaped into garage doors, gates and window grills. As he grew older, he became more and more interested in tinkering with things and building them himself, especially after he got a new toy – a hobbyist 3D printer.
It did not take long for Shashank to realise that 3D printing was his calling. After majoring in Materials from IISc for his undergraduate degree, he did his Master s from the University of California, Berkeley, where he studied Materials Science and Engineering. He is now with a San Francisco Bay Area company called Velo3D, a leading provider of metal 3D printing solutions. Shashank is among an entire generation of young people working on the technology of 3D printing or, to use the industry terminology, additive manufacturing (AM).
To illustrate the meaning of AM, it might be useful to understand how things are traditionally manufactured. The process typically involves fashioning raw materials into finished products using techniques that are subtractive in nature – material is removed from a solid block to achieve a desired shape, much like what a sculptor does with a hammer and chisel to create art.
AM, on the other hand, involves adding materials, layer by layer, to build something new, just as its name suggests. It is not unlike children building cars or houses with Lego bricks. AM does the same but with Lego bricks that are invisible to our eyes. The process begins by creating a digital 3D model, which is then fed into a specialised software. The software decides how best to virtually slice this model. Each slice is then printed, like in traditional 2D printing, and the layers are placed on top of each other to get the final product.
A new revolution
3D printing has gained much attention in recent years because it does not have the constraints of traditional manufacturing methods. Big tech giants are already realising its massive potential. General Electric has switched to AM jet engine parts to increase durability and save costs. Many international airlines, including Air India, are now using or have placed orders for LEAP engines in their aircraft. Developed by CFM International, LEAP is the first jet engine to include 3D-printed parts, making it lighter than conventional engines. These developments are transforming the aviation industry. It is no longer a toy. It is no longer a prototype technology. It is no longer meant just to make models or lookalikes, but there is an actual service part that is being made,” says Shashank.
3D printing has gained much attention in recent years because it does not have the constraints of traditional manufacturing methods
AM is also revolutionising space exploration. Terran 1, the first fully 3D-printed rocket developed by an American startup called Relativity Space was launched earlier this year. This rocket is made exclusively from 3D-printed parts, including the fuel tank and engine. NASA has also been exploring the use of 3D printing in space itself so that astronauts can manufacture tools and spare parts when required.
Small and medium manufacturers are also joining the bandwagon. For instance, this technology is being used by jewellers to make casting moulds for more intricate designs and by fancy restaurants to create designer food items. Customised 3D printers for chocolates and pasta are now available in the market. It is also being used to make plant-based and lab-grown meat. 3D printing holds great promise for printing organs for transplants and making skin grafts for burn victims. Entire houses are being built using concrete 3D printing technology. Not only does this reduce the cost and amount of raw materials used, it takes just a fraction of the time conventional construction methods require.
In addition to making new customised parts, AM is also being successfully used for repair and refurbishment of components in several engineering sectors. In the past, even if there was minor damage, quite often, the entire part would have to be replaced, because there was no technology to repair high-end materials, such as those used in the aviation sector. “It takes not just time, money, and effort, but there are no takers to repair small quantities of parts in a short period of time to cater to the need of the customer, says Dheepa Srinivasan, an alumna of the Department of Materials Engineering, IISc, currently with the Pratt and Whitney R&D Centre in the Institutes campus. According to her, AM is a panacea for bringing in innovative technology for difficult-to-repair parts, thereby extending the service life of components. She and her team are now working on new 3D-printed high temperature alloys for gas turbine engine applications, including nickel- and cobalt-based superalloys.
AM is also allowing researchers to revisit alloys which are difficult to manufacture using conventional methods and hence have not had practical applications. For instance, NASA is working on using a 3D-printed alloy called GRCop-42 in rocket thrust chambers and heat exchangers. This alloy retains high thermal conductivity and strength at high temperatures, crucial for heat transfer in rocket engine components. “The material has been around for 30-40 years, but existing fabrication methods just didn’t work. If you try to cast it, the material segregates. But today [with AM], it has become an extremely important material in the next generation of rocket engines,” says Shashank.
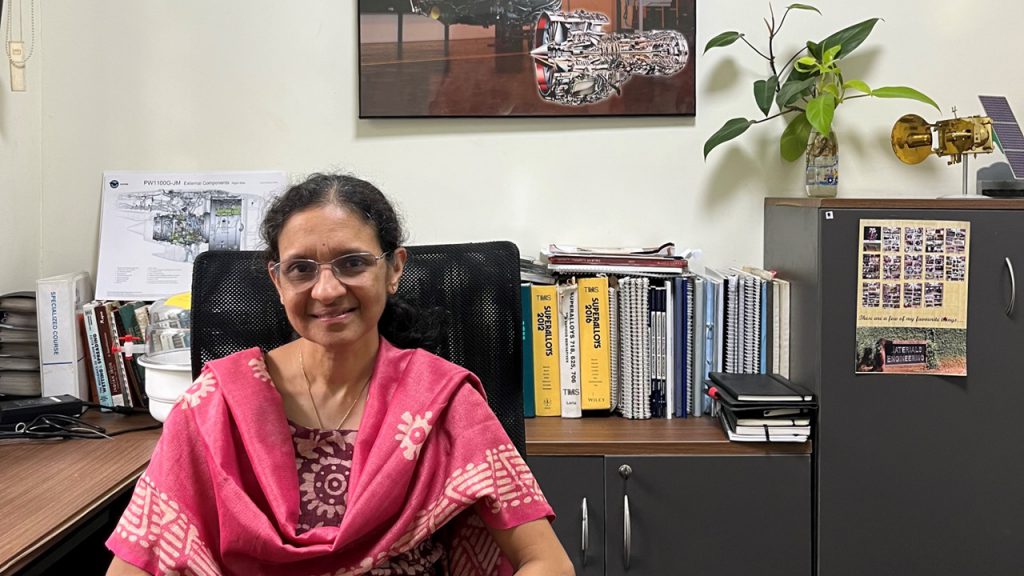
engine outlines in the background (Photo courtesy: Dheepa Srinivasan)
“3D printing has also paved the way for researchers to delve into nature-inspired designs,” says Amaresh Chakrabarti, Chair of the Centre for Product Design and Manufacturing (CPDM), IISc. For example, we are now better placed to mimic the properties of the bone, one of the wonders of nature. Bones are made up of porous tissues which makes them lightweight, yet incredibly strong. Like bones, there are several designs in nature that can be mimicked using 3D printing, he suggests.
Not surprisingly, 3D printing is now making inroads into the world of lightweight prosthetics and implants. Conventional prosthetics produced using casting are heavy. Using 3D printing, it is now possible to design anatomy-specific devices for the patients, which are both customisable and
lightweight. Such devices can dramatically improve the quality of life for millions of patients. It can be a great boon for both the clinicians as well as the patients, says Dheepa, who has also worked closely with doctors and rehabilitation centres, “to provide timely, restorative, custom-made 3D-printed solutions for the patient population.”
IISc joins the race
Recognising the increasing role of this revolutionary technology, IISc has taken many steps to encourage research and innovation in 3D printing. In 2019, CPDM started an MTech in Smart Manufacturing, and AM is an integral part of this programme.
Funded by Wipro 3D and the Department of Heavy Industries, Government of India, IISc has successfully built an electron beam metal 3D printer, which is ready to be marketed. It is the result of a collaboration between multiple departments, each bringing in its own expertise and resources. This equipment can be customised to accommodate different research requirements. For instance, thermal cameras and sensors can be added to it, which is not possible with machines currently available in the market.
One of the advantages of AM is that researchers and innovators can combine different materials to fabricate complex designs. And this is what HEM Dimensions Private Limited is doing at the Foundation for Science, Innovation and Development (FSID) in IISc. The startup was established by Hemang Kumar Jayant, a former PhD student at CPDM, in 2022. His team is working on multi-material AM that combines metals and polymers for printing smart electronic devices. One of their success stories is a device for real-time monitoring of heart activity. The metal and polymer materials are printed in layers sequentially to create functional electronic devices in one shot using a hybrid AM machine that his team has developed. “The hybrid AM machine will cut down the prototyping time significantly,” says Chakrabarti.
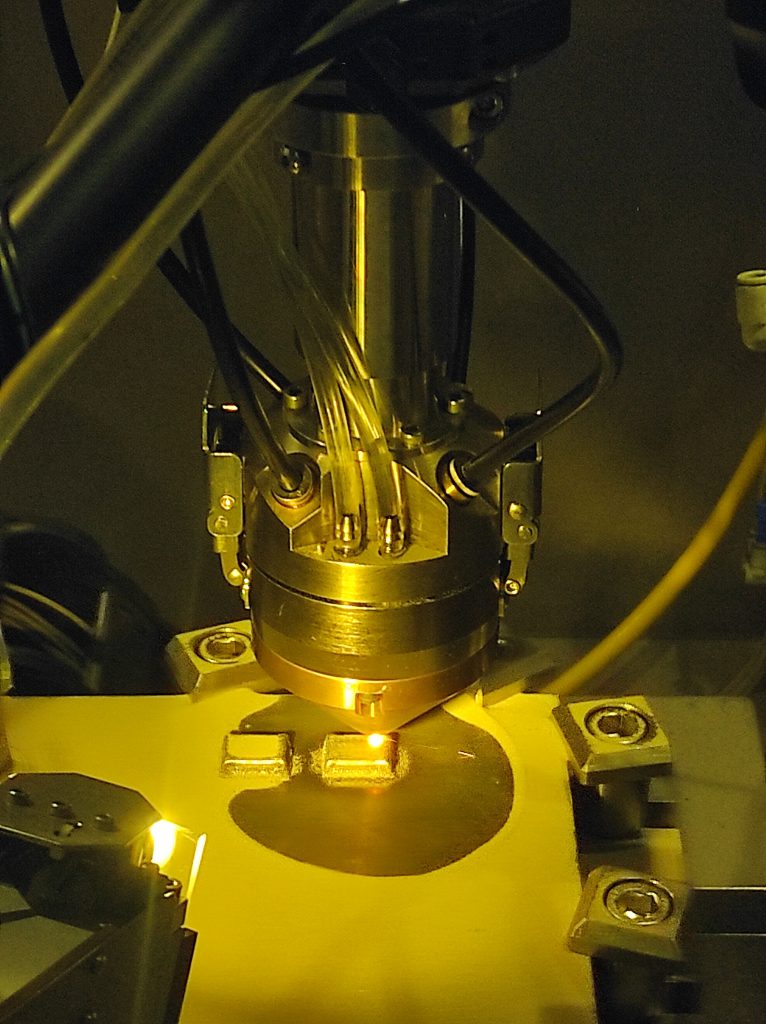
Dineshkumar Harursampath, Associate Professor in the Department of Aerospace Engineering, IISc, believes that multi-material AM technology will revolutionise the way we make things. “Customising structures with highly complex geometries and multiple material distributions will become a child’s play with AM.”
Dineshkumar’s lab is involved in yet another exciting project on materials called auxetics. When conventional materials like rubber bands are stretched, they become thinner. But auxetics, paradoxically, become thicker when stretched. The potential applications of auxetics are endless – as shock absorbers in body armours, as sound absorbers, as shoes that fit perfectly. But they are not easy to make and, therefore, are not yet used commercially. That, however, may be changing because of the AM revolution, according to Dineshkumar. “Built from repeating patterns, auxetics, by design, are best suited for AM. To mention a few potential applications [in the aircraft industry alone], this will be suitable for
aircraft seat frames and luggage bins.”
His team is also attempting to use 3D printing to reduce carbon footprint. “AM has the potential to contribute to sustainable manufacturing practices.” They are exploring ways to develop efficient recycling methods for AM-produced parts, thus reducing material wastage, energy consumption and carbon emissions.
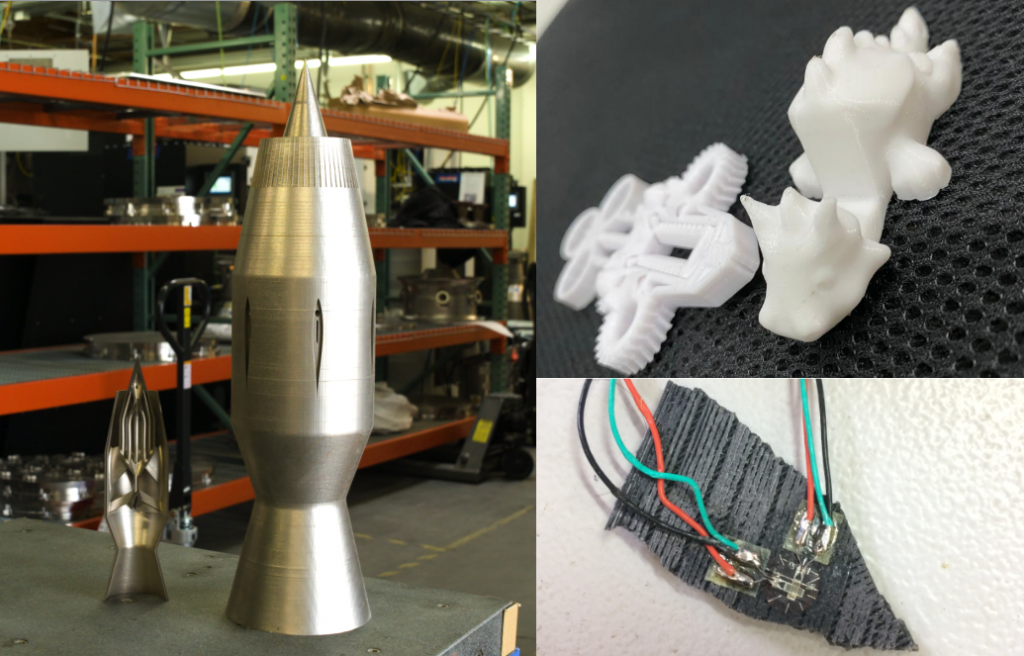
3D-printed plastic parts; Bottom right: 3D-printed auxetic composite
being tested
(Photos courtesy: Shashank HR, Subhodeep Jana, Dineshkumar Harursampath)
Challenges
However, several hurdles need to be overcome before AM realises its full potential. For one, raw materials for metal AM are expensive. Researchers at IISc are working on developing metal powders that are cheaper and more energy efficient. These powders have very similar characteristics to the commercially available powders, but could be produced at a fraction of the cost. Besides, the process of 3D printing itself is currently too expensive for mass production.
Moreover, unlike conventional manufacturing processes, it builds one layer at a time and hence is slow.
There are also some myths surrounding AM which need to be debunked, according to Chakrabarti. One of them is that extremely high-quality powder is needed to produce high-quality finished products. “We throw in different sizes of powders and see what kind of quality comes up. And it turns out that the quality is not that different,” he says. Such parts made with powders of different sizes may not always be suitable for niche applications such as in the aerospace industry, but are more than adequate for consumer applications such as customised jewellery.
There are also some myths surrounding AM which need to be debunked
Chakrabarti highlights yet another challenge: 3D printing requires a different kind of expertise. “Some of the earlier wisdom about how you make things gets thrown out of the window and you have to do things differently,” he says. “So how do you change your design such that it is better amenable to being printed in an additive manner?” he asks rhetorically. 3D printing consists of melting a tiny piece of a material, one at a time, and glueing them together. “If you increase speed, then these little pieces will have less time to attach with each other. If you slow down too much, there will be too much energy, they will evaporate or they will remain molten or even melt the material that has already solidified. It will change the properties. So, you must find the right balance between the two.”
While researchers and innovators are confident of overcoming many of these challenges, Dineshkumar offers a word of caution. He says that despite its promise, the new technology cannot replace traditional manufacturing entirely. Instead, he envisions a future in which AM and Subtractive Manufacturing (SM) will work hand-in-hand in a synergistic manner leveraging the benefits of both, while minimising their deficiencies. “Addition and subtraction are an integral part of how nature makes things.”
Soumya Mishra is a PhD student in the Department of Materials Engineering, IISc and a science writing intern at the Office of Communications